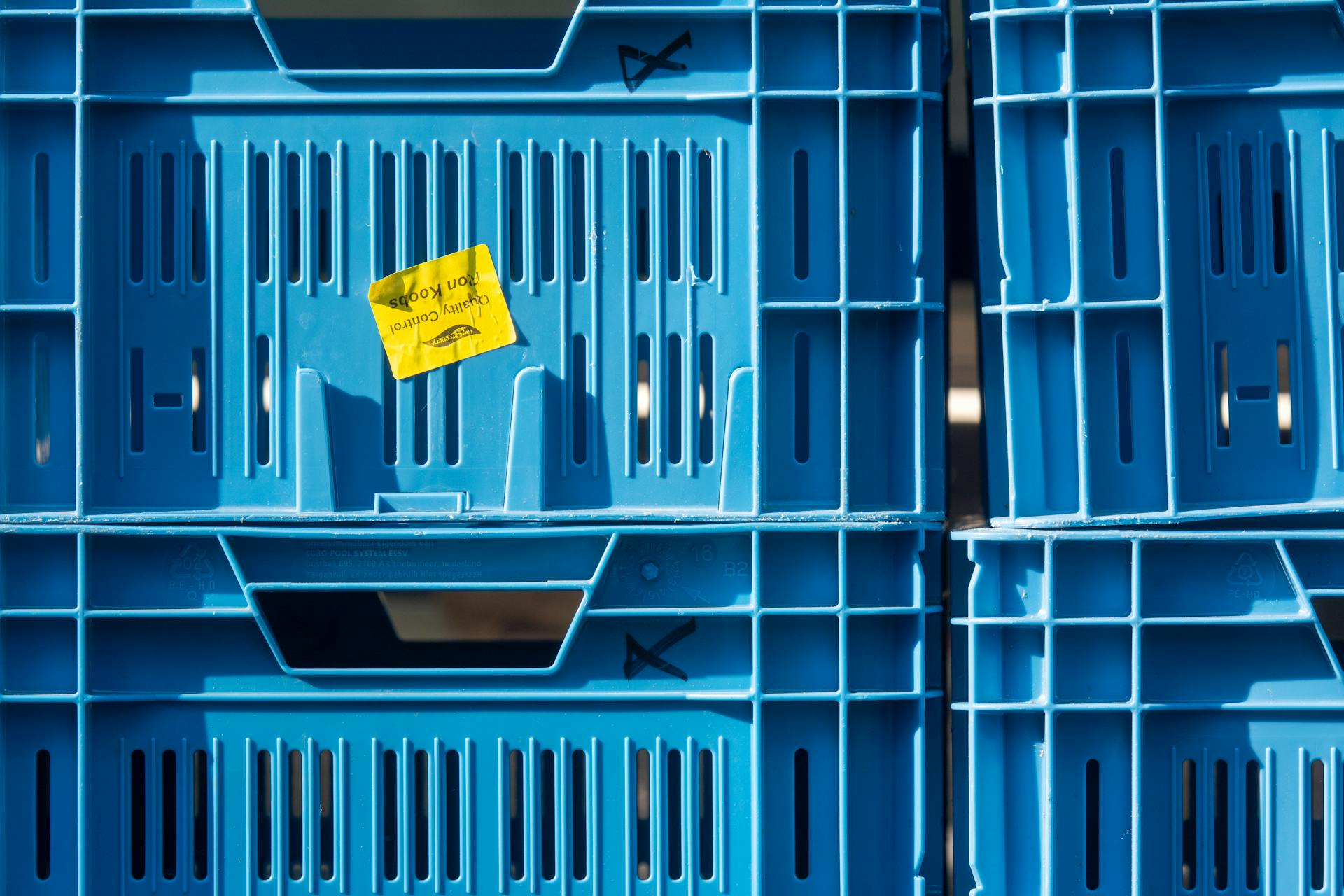
Quality control is crucial for companies to thrive in today's competitive market. A single mistake can lead to a loss of customer trust and ultimately, a decline in sales.
According to a study, 70% of consumers are more likely to do business with a company that has a reputation for quality. This is a clear indication of the importance of quality control in building customer loyalty.
Companies that prioritize quality control have a significant edge over their competitors. They are able to deliver products that meet or exceed customer expectations, leading to increased customer satisfaction and loyalty.
In fact, a company that implements effective quality control measures can see a 25% increase in sales within the first year. This is a tangible benefit that can be achieved through a focus on quality control.
For another approach, see: Why Is Culture Important in a Company
Why Quality Control Matters
Quality control is the linchpin that determines the success of any manufacturing process. It ensures consistency, reliability, and adherence to specifications, fostering a reputation for reliability and trust.
Recommended read: Why Is Reliability Important
Manufacturers are under constant pressure to reduce waste and eliminate inefficiencies, and quality control is an essential way to track requirements and assign standards. Quality control teams measure performance against these standards, and then address core quality issues such as variability, volatility, and unpredictability.
Without quality control, production lines could stand still, and manufacturers risk everything – reputation, sales prospects, and profitability. Quality control is not just about fixing issues, but also about revealing magnitudes of opportunity.
Products with superior quality gain a distinct edge in a fiercely competitive market, leading to increased customer loyalty and brand recognition. Manufacturers can use data they already collect to advance their organizations, not just defend and protect them.
Check this out: Why Is Version Control Important
Benefits of Quality Control
Implementing quality control in manufacturing is a no-brainer. It yields a plethora of advantages, ranging from enhanced customer satisfaction to increased operational efficiency.
Quality control helps prevent lawsuits by producing reliable products that work correctly. This reduces the risk of liability and shows that the company is taking necessary measures to ensure safety and quality.
Here's an interesting read: Is Post Control Important 2k24
Detecting and rectifying defects early in the production process minimizes waste and reduces operational costs. This proactive approach contributes to cost savings and bolsters overall efficiency.
Implementing quality control at every production stage reduces the chances of delays, as errors are quickly detected and rectified. This makes production more economical and helps prevent the hassle of returns and associated costs.
By using quality control practices, manufacturers can prevent inconsistencies or other failures that delay operations. This enables production lines to run smoothly and close to capacity, increasing overall productivity.
Here are some key benefits of quality control:
- Enhanced customer satisfaction
- Increased operational efficiency
- Reduced risk of liability
- Minimized waste and reduced operational costs
- Increased productivity
Quality Control Process
A quality control process is a set of steps arranged in order, detailing exactly how a task should be performed. This helps businesses scale and ensures consistent outcomes with little to no variation in the end product or service delivery.
Processes serve as a checklist for employees, allowing them to review process documentation against the steps they executed to self-audit. By creating processes, businesses can make it easier for new team members to become productive and efficient quickly.
You might enjoy: Why Is It Important to Support Local Businesses
Here are some key steps involved in a quality control process:
- Manufacturing quality control personnel ensure that goods meet specific standards.
- They pull samples of product from batches and test their composition, physical properties, and other metrics to make sure it meets regulations.
- Final product inspection guarantees that only items meeting stringent quality criteria reach the market.
By implementing quality control processes, businesses can improve customer satisfaction, increase word of mouth, and boost the quality of their products and services.
During Data Collection
During Data Collection, it's common for quality information to be gathered, but not in a format that's easy to access or analyze. Metrics may be stored on paper or only be available onsite.
Gathering quality information in a non-standard format can lead to discrepancies, such as using different naming conventions for quality inputs, like ingredient names or measurements. This can make it difficult to compare data across different processes or locations.
Manufacturing quality control personnel often check measurements and results only periodically, which can lead to issues going undetected for too long. This can be especially problematic if manual calculations are used to determine performance metrics, as human errors can occur.
Here are some common challenges that can arise during data collection:
- Gather quality information, but not in a format that’s easy to access or analyze.
- Use different naming conventions for quality inputs, such as ingredient names or measurements.
- Check measurements and results only periodically.
- Manually calculate performance metrics.
- Address quality issues with home-grown solutions that aren’t replicable or that rely upon a particular person.
By collecting and storing all quality data in a standard format—and in a centralized location—organizations can ensure that their data is comparable across the business and for a variety of use cases.
Analyzing Data
Analyzing quality control data can be a daunting task, especially when there's too much of it to sift through. Manufacturers often struggle to troubleshoot issues in the moment or test "what if" scenarios without a lot of manual work or risk.
They may only look at historical performance data when there's an issue or an external request, but this can lead to missed opportunities for improvement. Prioritizing data collection, compliance, and storage tasks over analysis can also hinder progress.
Trying to use control charts to answer all quality control questions can be time-consuming, as it involves reformatting and manipulating data to meet different users' needs or customer data requests. This can lead to frustration and wasted resources.
But with the right tools, manufacturers can have data sorted and sifted automatically, and pertinent reports are accessible within a few clicks. They can see quality control data in real time, and retrieve historical information from the same platform – without juggling spreadsheets.
Reports can be customized for different use cases in the organization, providing users with exactly what they need, when they need it – in a format they can understand and use right away.
Readers also liked: Why Is Bandwidth Important to Internet Users
Implementing with SweetProcess
Implementing quality control processes is a crucial step in ensuring the quality of your products and services. By creating processes that outline the steps to complete a task, you can establish a standard for work and keep it there.
SweetProcess is a tool that makes it easy to create detailed processes containing images or screenshots that let your team members know exactly what is required of them. This helps to reduce errors and improve efficiency.
With SweetProcess, you can create processes once and then be done with them, except to update or refresh them. This saves time and resources, and ensures that everyone who performs a role performs it according to the standard.
Here's a step-by-step guide on using SweetProcess to implement quality control:
- Create detailed processes containing images or screenshots that outline the steps to complete a task.
- Assign processes to team members to ensure they know what is required of them.
- Review and update processes regularly to ensure they remain effective.
- Use SweetProcess's suite of tools to create policies and knowledge bases that boost the quality of your products and services.
By following these steps, you can implement quality control processes that improve customer satisfaction and increase word of mouth about your product quality. With SweetProcess, you can easily create and manage processes, policies, and knowledge bases to boost the quality of your products and services.
Quality Control Methods
Quality control methods are essential for businesses to ensure they're producing high-quality products or services. The Taguchi method, for instance, is a preemptive strategy to minimize defects and variations in the end product.
Genichi Taguchi believed that preemptive quality control measures during research, design, and development of processes were critical to creating uniformity in product quality and performance. This approach can be applied to various industries, including content creation.
Pareto charts are a useful tool for identifying the most important levers of profit and the most important causes of pitfalls in the production process. By visualizing these key areas, businesses can conserve human resources and reduce waste.
The Pareto principle states that 80% of the results come from 20% of efforts, which can be applied to a company's product line or service delivery. For example, 20% of a company's product line may be responsible for 80% of its revenue.
Fishbone diagrams, also known as Ishikawa diagrams, are tools used to find the root causes of problems. By analyzing the problem along the lines of methods, machines, people, materials, measurement, and environment, businesses can identify the underlying causes of issues.
See what others are reading: Why Are Values Important in a Company
Checklists are a simple yet effective way to audit processes and verify that every necessary step has been completed. This approach allows for team-wide autonomy and ensures compliance with quality standards.
Six Sigma is a framework that focuses on reducing product defects using statistical methods. This approach is most relevant to industries like manufacturing and engineering, where precision and accuracy are crucial.
SweetProcess is a versatile suite of tools that can help businesses improve customer satisfaction by creating processes, policies, and knowledge bases to boost the quality of their products and services.
Frequently Asked Questions
What are the three main objectives of quality control?
The three main objectives of quality control are to improve product quality, increase production efficiency, and build customer loyalty. By achieving these objectives, businesses can reduce risks and enhance overall performance.
What are the five responsibilities of quality control?
Quality control involves inspecting and testing products to ensure they meet production standards, recommending process adjustments as needed, and measuring materials and products accurately. Key responsibilities include reviewing blueprints, monitoring operations, and inspecting products with precision tools.
Why is quality checklist important?
A quality checklist is crucial as it ensures products meet standards, reducing waste and boosting customer satisfaction. By implementing a quality checklist, manufacturers can improve overall quality and communication.
What is the purpose of data quality checks?
Data quality checks aim to verify the accuracy, completeness, and relevance of data to ensure it's reliable and trustworthy. This helps maintain the integrity of data and supports informed decision-making.
Sources
- https://www.advantive.com/solutions/spc-software/quality-management/quality-management-quality-control-in-manufacturing/
- https://www.eastwestbasics.com/the-importance-of-quality-control-in-manufacturing/
- https://medium.com/@amrepinspect5/why-is-quality-control-important-in-manufacturing-a-complete-guide-590ac8bc7608
- https://www.sweetprocess.com/quality-control/
- https://www.aerotek.com/en/insights/quality-control-in-manufacturing
Featured Images: pexels.com