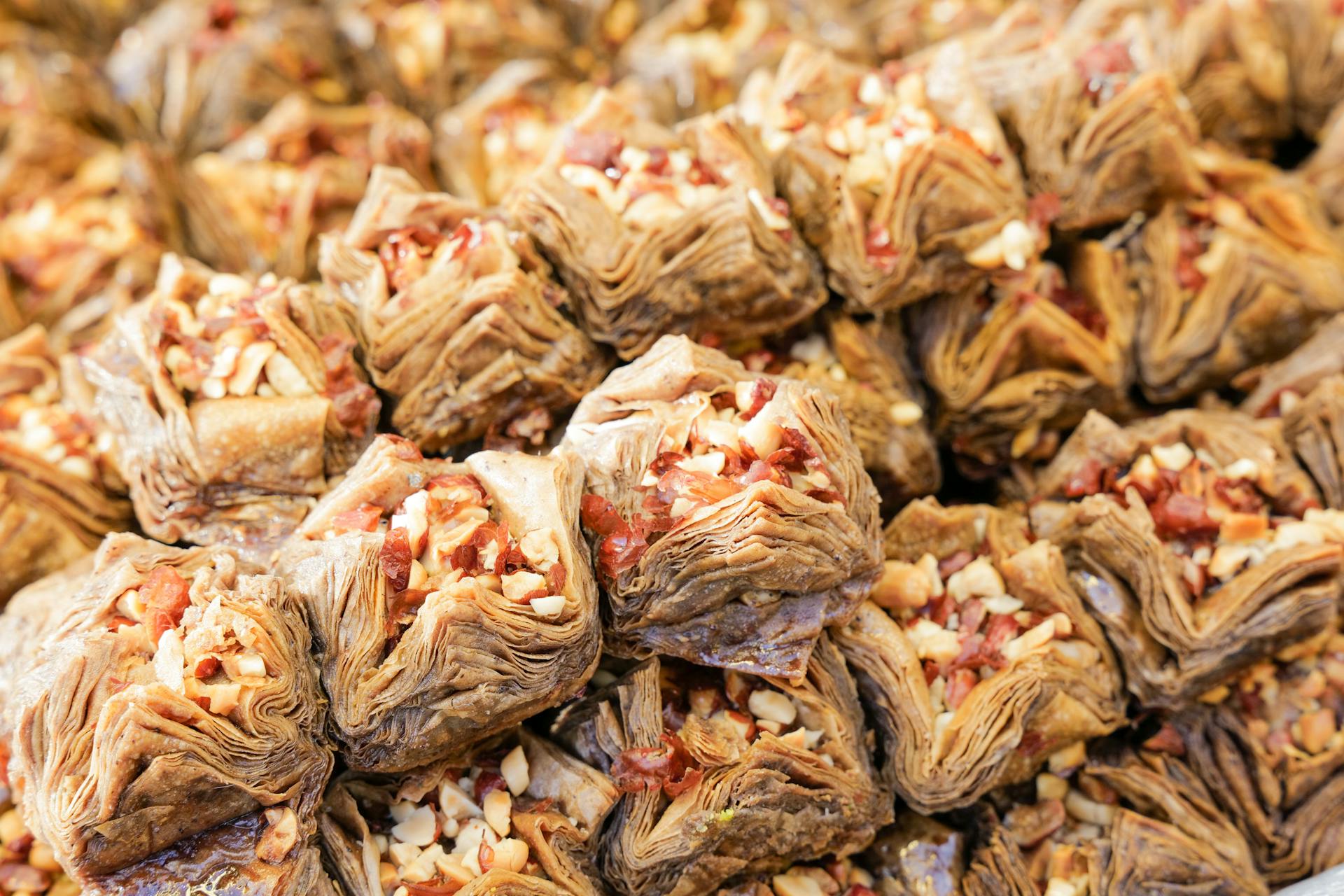
FIFO, or First-In-First-Out, is a crucial concept for efficient supply chain management. This means that the oldest items in inventory are sold or used before newer ones.
By implementing FIFO, businesses can avoid stockouts and overstocking, which can lead to significant losses. In fact, a study found that companies that use FIFO have a 20% lower inventory turnover rate compared to those that don't.
FIFO helps to prevent product degradation, which can occur when older items sit on shelves for too long. For example, perishable goods like food and medicine have a shorter shelf life and must be sold before they expire.
Implementing FIFO requires careful tracking and monitoring of inventory levels. This can be done using inventory management software or manual tracking methods.
What Is the First In, First Out Method
The First In, First Out method is a system used to manage inventory, where the oldest items are sold or used first. This ensures that products with a shelf life are sold before they expire.
Many industries, including food service and manufacturing, rely on the FIFO method. This process helps businesses stay compliant with Good Manufacturing Practices (GMPs).
The FIFO method is widely used because it prioritizes consumer safety. Businesses can track their inventory using software programs that follow this method.
Importance of FIFO
FIFO is a widely used method to account for the cost of inventory in your accounting system, and it's the easiest inventory method to implement and use.
Using FIFO can help you sharpen your profit and COGS calculations, reduce losses, and unlock actionable insights regarding product demand. By adopting a FIFO approach, you can reduce losses and gain a better understanding of your profit margins.
FIFO helps mitigate complications in accounting accuracy, allowing you to maintain a precise understanding of your profit margins. This is especially important when the costs of goods and materials change over time.
FIFO is a must for businesses that sell perishable items, such as food or medicine, as it provides the most accurate inventory and sales profit calculation. It's also ideal for companies that engage in international business, as it's one of the few options permitted under International Financial Accounting Standards (IFRS).
Here are some businesses that can benefit from FIFO:
- Businesses that use a periodic inventory system
- Companies that sell perishable items
- Companies that engage in international business
By using FIFO, you can demonstrate a better value to potential buyers, especially when seeking investor support or planning to sell your company. This is because FIFO helps balance your COGS in relation to your profits, ensuring that you sell the oldest stock first and help balance your COGS in relation to your profits.
Implementing FIFO
Implementing FIFO requires the right equipment, such as gravity flow racking or pallet rack systems, to facilitate the flow of goods. These systems allow teams to feed goods into one side of the rack and retrieve them from the other, making it easier to implement the first in, first out principle.
Training staff in the FIFO principle is also crucial, as it can take time for them to get accustomed to the new stocking strategy. To track product entry and exit dates, dynamic inventory management software is essential, as manual recording can lead to accounting errors.
To successfully implement a FIFO system, it's essential to have a system in place for tracking and recording inventory activities in real-time. This can be achieved through automation, such as using barcode or RFID technology, and developing a system for tracking, recording, and analyzing inventory data.
Here are some key steps to implement a FIFO system:
- Establish well-defined goals and objectives for FIFO-based inventory control and management.
- Embrace automation by leveraging barcode or RFID technology.
- Develop a system for tracking, recording, and analyzing inventory data to ensure efficiency and identify opportunities for improvements.
- Create buy-in among staff to ensure the FIFO system is fully adopted and set up for success.
Best Practices
Implementing FIFO requires attention to both accounting and inventory management. Using accounting software that has an inventory management component can make cost analysis easier and more efficient.
You should think about inventory flow to ensure the first inventory is sold first, especially when managing perishable goods. This is crucial because the first in will also be the first to go bad.
Inputting inventory the day you receive it is best practice. This helps match inventory to purchase orders and automatically calculates costs when items are sold.
Here are some key best practices to keep in mind:
- Use accounting software that has an inventory management component.
- Think about inventory flow, especially for perishable goods.
- Input inventory the day you receive it.
Implementing in Warehousing
Implementing FIFO in warehousing requires the right equipment, including gravity flow racking or pallet rack systems. These systems allow teams to feed goods into one side of the rack and retrieve them from the other.
To implement FIFO, you'll need to train your staff in the first in, first out principle. While it's a relatively simple approach, it can take some time for your team to get accustomed to the new stocking strategy.
You'll also need dynamic inventory management software that tracks product entry and exit dates. This is crucial for accurate accounting and preventing errors.
A good inventory management platform will assist with everything from average inventory accounting to tracking losses and running analytics reports. It will also help you hold inventory, keep up with stock levels, and tailor your reordering strategy.
Here are some key features to look for in an inventory management platform:
- Tracks product entry and exit dates
- Assists with average inventory accounting
- Tracks losses
- Runs analytics reports
- Helps with inventory holding and stock level management
- Tailors reordering strategy
By implementing these features, you'll be able to improve your inventory management and reduce costs.
Advantages of the Method
The FIFO method is a popular inventory management approach that offers numerous benefits to businesses. It allows for accurate cost analysis, which is essential for making informed decisions about inventory levels and pricing.
Many accounting software options, including QuickBooks, only use the FIFO method to account for inventory. This means that if you want to use a more complicated method, you'll likely need to find an expensive software or outsource your accounting.
Using the FIFO method can also help you unlock actionable insights regarding product demand. By tracking the cost of each unit of inventory, you can identify trends and patterns that can inform your inventory management strategies.
FIFO provides the most accurate picture of what your inventory is costing the business at any given time. This leads to better accounting and more real-time analysis on where the business stands if it has a heavy amount of inventory.
Here are some of the key advantages of the FIFO method:
- Accurate cost analysis
- Software compatibility
- Easy to use and apply
- Higher profit calculation
The FIFO method is a straightforward way to calculate COGS, but it can be time-consuming if a business has extensive inventories. However, with the right software and systems in place, it can be a simple and effective way to manage your inventory and improve your bottom line.
Comparison with LIFO
FIFO is often compared to LIFO, a method that's essentially FIFO flipped around. LIFO stands for last in, first out, and it assumes the last inventory purchased is the first to be sold.
The main difference between FIFO and LIFO is how they affect financial statements and inventory valuation. LIFO can be more beneficial during times of inflation because it lowers your net profits and taxable income.
Businesses using LIFO will record the most recent inventory costs first, which impacts taxes if the cost of goods in the current economic conditions are higher and sales are down. This means LIFO could enable businesses to pay less income tax than they likely should be paying.
However, FIFO does a better job of calculating taxes, making it a more accurate method for inventory valuation. LIFO is only legally used by U.S.-based businesses, but it's not the most common method used.
In some industries, like the auto industry, LIFO makes sense due to the nature and movement speed of their inventory. Businesses in the U.S. can use the LIFO method if they fill out Form 970, but it's essential to understand the nuances of both methods before selecting the right one for your business.
Example and Recommendations
Let's take a look at how FIFO works in a real-world example. A clothing store buys 100 shirts for $5 each, then adds 50 more shirts for $6 each, bringing the total to 150 shirts. After selling 80 shirts, the store is left with 70 shirts, valued at $400 ($100 + $300).
To make FIFO a routine, follow these simple tips: rotate existing inventory forward and put newest boxes in the back of the cooler, and always pull boxes from the front first when re-stocking. This ensures that older products are sold before newer ones. Consistently culling, consolidating, and rotating product will keep displays fresh, full, and selling.
Here's a quick rundown of FIFO best practices:
- Rotate existing inventory forward and put newest boxes in the back of the cooler.
- Pull boxes from the front first when re-stocking.
- Cull all displays before bringing new product to the sales floor, removing out-of-date or unsellable items.
- Consolidate bouquets or bunches of older products and move forward.
- Perform culling, consolidation, and rotation daily or more, depending on sales volume.
Example
Let's dive into an example of how FIFO works in a real-world scenario. A clothing store buys 100 shirts at $5 each, totaling $500 in beginning inventory.
The store then purchases an additional 50 shirts at $6 each, adding $300 to the inventory. This brings the total shirts to 150 and the total inventory cost to $800.
Throughout the grand opening month, the store sells 80 shirts. Under the FIFO method, all 80 sold shirts would have been from the first 100 lot purchased.
Recommendations
To make FIFO a routine that becomes second nature, follow these consistent recommendations:
Rotate existing inventory forward and put newest boxes in the back of the cooler after receiving new product and completing quality control checks.
Before bringing new product to the sales floor, cull all displays checking sell by dates and removing all product that is out of date or not sellable.
Consolidate bouquets or bunches of older products and move forward, placing the oldest product on the first tier or floor closest to the customer.
Newest product should be placed behind older product, usually on the highest tier and furthest away from the customer.
Culling, consolidation, and rotation of product should be performed at a minimum once daily or more depending on sales volume to keep displays fresh, full, and selling.
Here's a summary of the FIFO rotation:
- Put newest boxes in the back of the cooler.
- Remove out-of-date or unsellable product from displays.
- Consolidate older products and move them forward.
- Place newest product behind older product.
- Cull, consolidate, and rotate product daily or more often if necessary.
Frequently Asked Questions
Why do most companies use FIFO?
Most companies use FIFO because it provides an accurate picture of inventory costs by aligning expected and actual cost flows. This makes it the most widely used and accurate method globally for valuing inventory.
Sources
- https://www.fishbowlinventory.com/blog/optimizing-the-fifo-method-for-effective-inventory-management
- https://safetyculture.com/topics/inventory-management-system/fifo-method/
- https://www.smartwarehousing.com/blog/what-is-fifo-and-why-is-it-vital-for-good-inventory-management
- https://www.forbes.com/advisor/business/fifo-method/
- https://floralife.com/article/fifo-what-is-it-why-is-it-important/
Featured Images: pexels.com