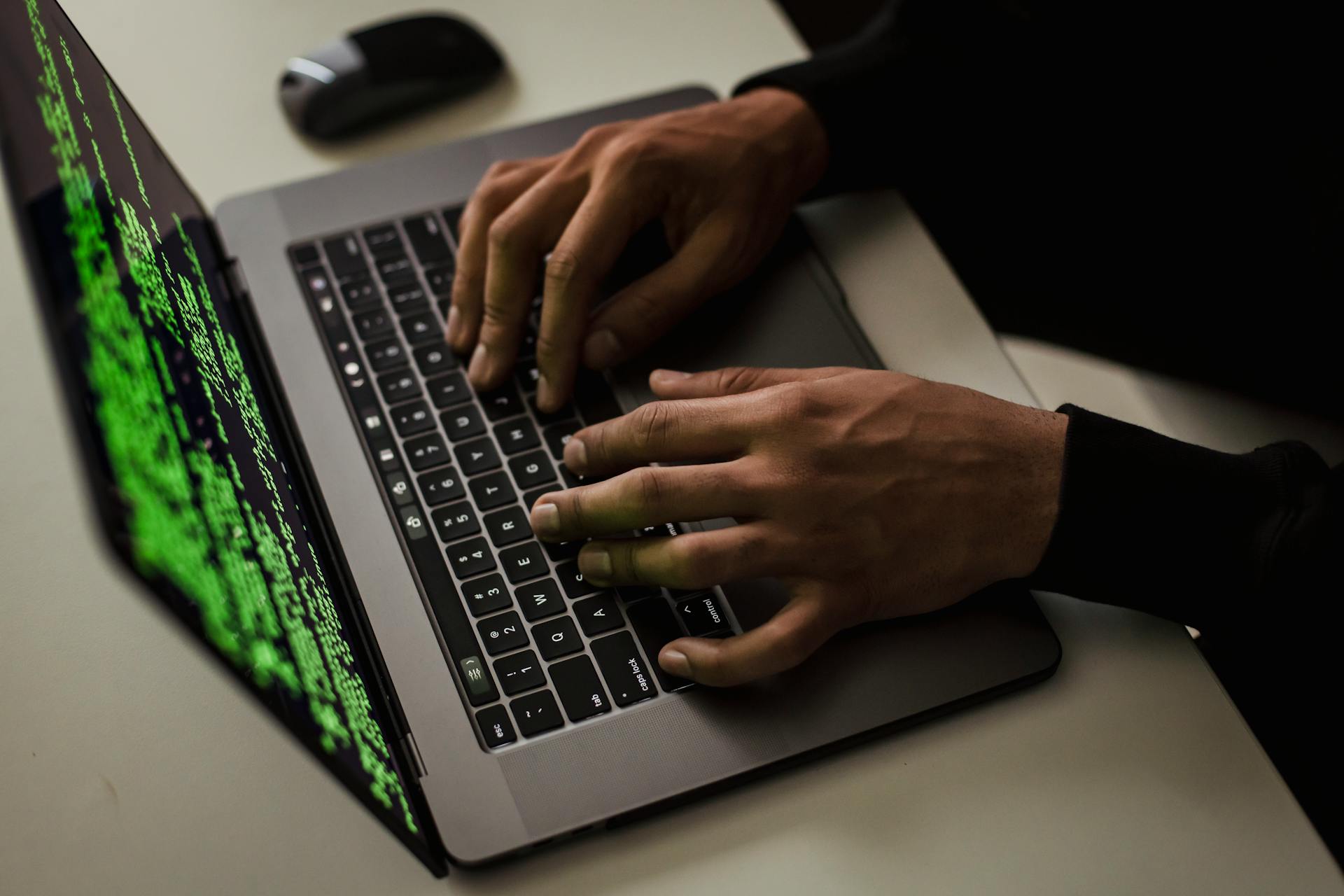
Computer numerical control (CNC) is a revolutionary technology that has transformed the manufacturing industry over the past few decades. With the help of CNC machines, manufacturers can automate and streamline their production processes, resulting in higher efficiency and accuracy. CNC machines are programmed to execute precise movements and operations on various materials such as metal, plastic, wood, and composites.
In simple terms, CNC is a process where a computerized system controls the movement of cutting tools or other machinery in order to produce complex parts with high precision. The computer reads a code that instructs it how and where to move the tool or workpiece. This code consists of numerical values that represent different parameters like speed, direction, depth of cut, etc. By utilizing this technology, manufacturers can create intricate designs or parts that would be impossible to achieve manually.
For your interest: Why Is the Technology Important
An Easy Way to Learn about CNC: A Brief Overview
CNC, or computer numerical control, is a system that uses software to control machines. In this system, the movements of a machine are based on code obtained from an original 3D model. Numerical controls describe the various CNC movements, which can be executed using servo motors.
One important aspect of CNC is the rotating part where the tool holder is located. This tool holder can hold multiple tools, which enables different types of operations to be performed on a workpiece. To run the machine, CNC operators monitor machines and ensure that they are running smoothly.
CNC programmers create the code that runs these machines. This code specifies how the machine should move and engage with the workpiece. With CNC, it's easy to replicate parts quickly and with precision since the entire process is automated. Overall, learning about CNC can provide individuals with insight into how manufacturing processes work in modern industries today.
CNC Systems: The Key Players in Various Industries
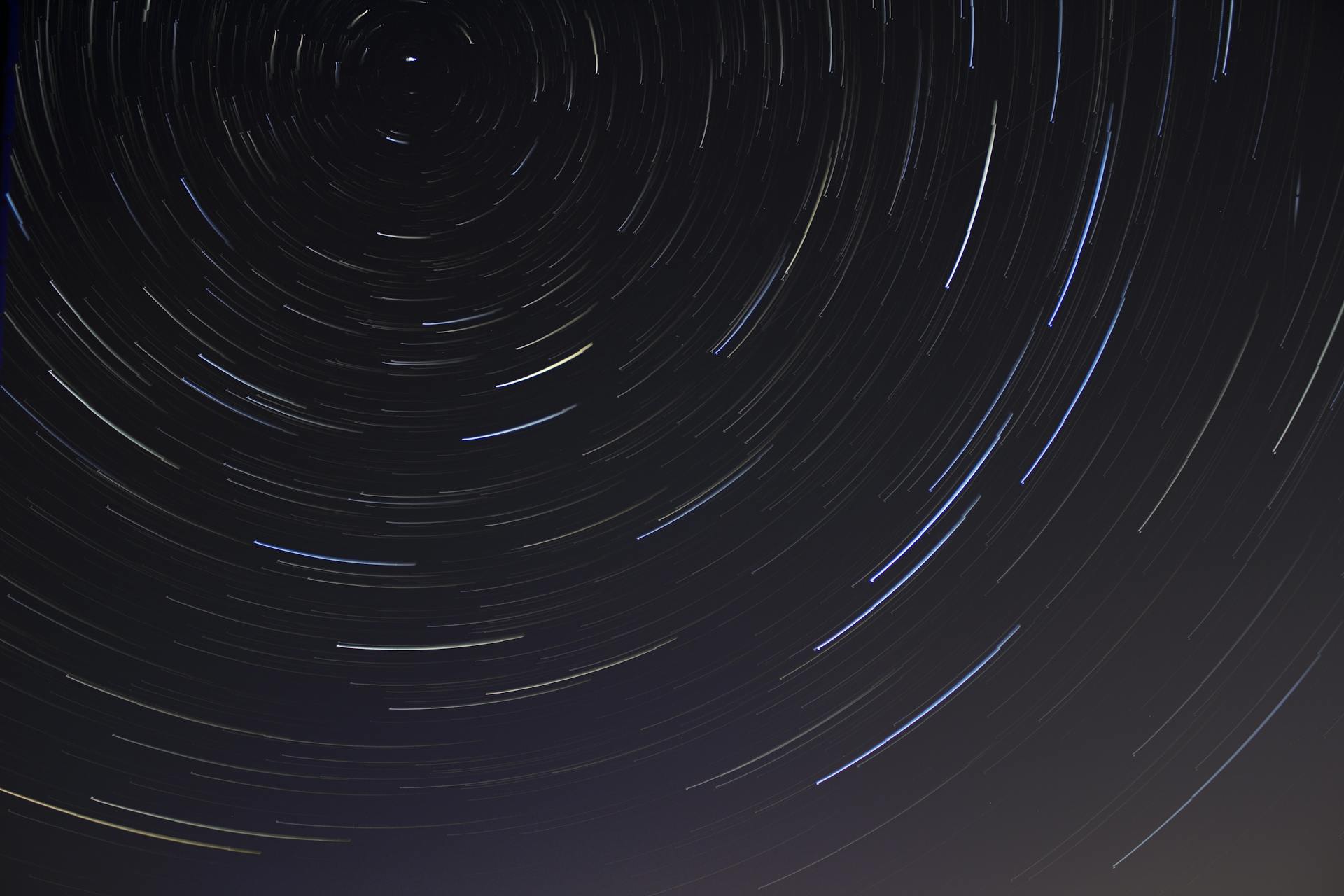
CNC systems are the backbone of modern manufacturing processes. Computer numerical control systems directly create the companies final product, and cnc technologies can be found in various industries including the automotive industry, aerospace industry, electronics industry, construction industry, architecture industry, furniture industry, healthcare industry, dental industry, textiles industry, military industry, aviation industry, shipbuilding industry, wood working industry, metal fabrication industry and even the recreation and robotics industries.
One of the main reasons why CNC systems are so popular is because they offer precision and accuracy in a way that just isn't possible with traditional manufacturing processes. This means that companies can create products that are more intricate and complex than ever before. From jewelry to signage to sports equipment to industrial machinery to gas pipelines - CNC systems can be seen everywhere.
Another major advantage of CNC systems is their ability to automate tasks. This means that jobs that once required manual labor can now be performed quickly and efficiently with little to no human intervention. This has led to increased productivity across many industries including the semiconductor industry, packaging industry, plastics industry, glass industry and beverage industry. Additionally, automation has made it possible for companies to reduce waste and improve quality control - ultimately resulting in cost savings for both manufacturers and consumers alike.
Discover the Intriguing Way CNC Technology Operates
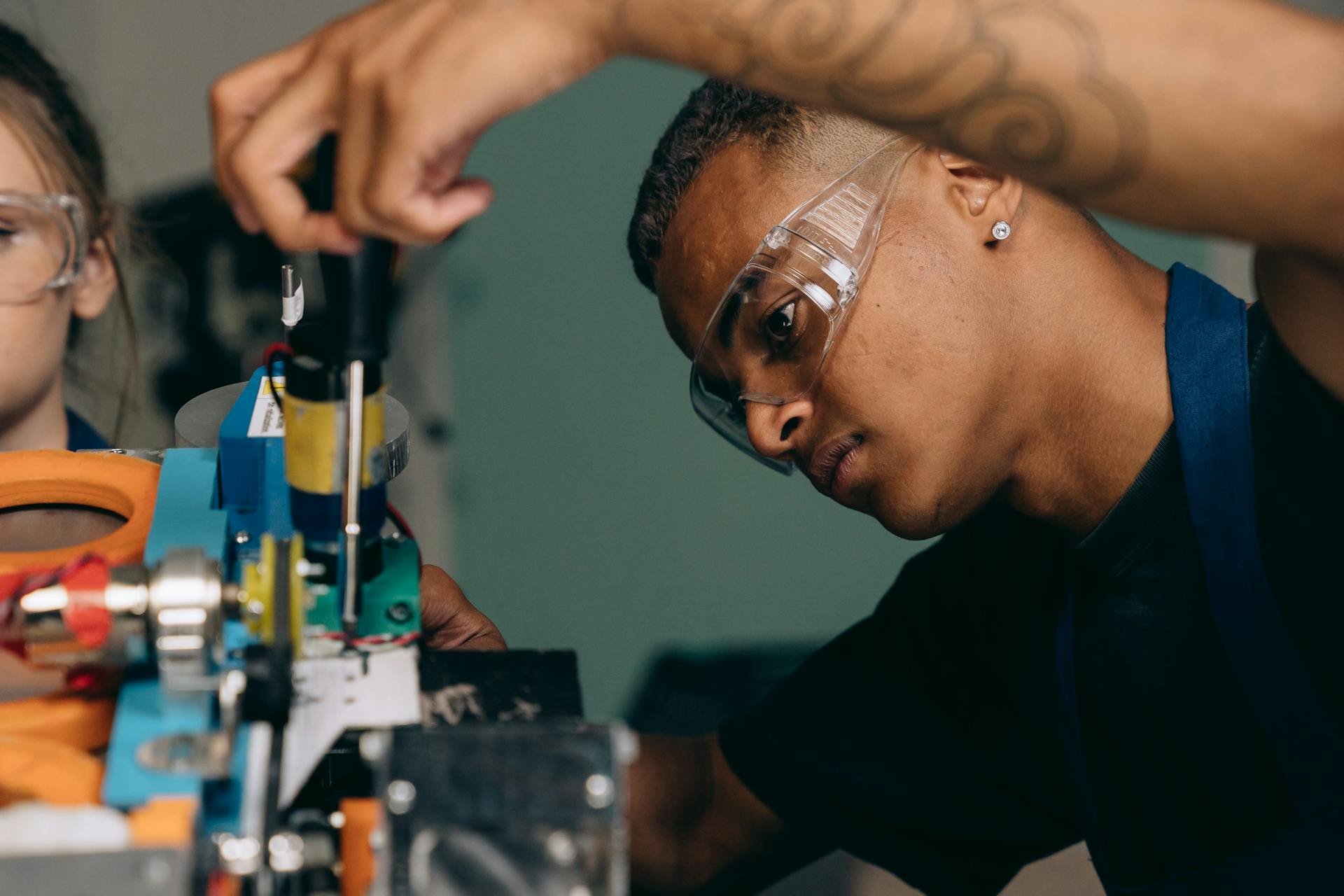
Are you curious about how CNC technology operates? It's a fascinating process that combines computer-aided design (CAD) software and computer numerical control (CNC) components to create an intricate manufacturing system. First, designers use unique CAD programs to create a part made of 3D shapes and surfaces.
Next, the resulting files are edited with specific values that translate into CNC machine-understandable language. This required process is minor in comparison to the impressive results it produces. These resulting files, called Computer Aided Manufacturing (CAM) models, are then sent to the CNC machine for production. The CNC components cut and shape materials precisely according to the CAM models, creating parts with incredible accuracy and speed.
Readers also liked: How to Store Files in the Cloud
1. What is the Coordinate System for CNC Machines?
The coordinate system for CNC machines is based on the Cartesian coordinate system, with axes parallel to each other and perpendicular to the worktable termed as X, Y, and Z. Additionally, some CNC machines have additional axes called a-axis and b-axis which allow for rotary axis motion perpendicular to the main three axes. Understanding these concepts is crucial for programming and operating CNC machines effectively.
Different Computer Numerical Control Software
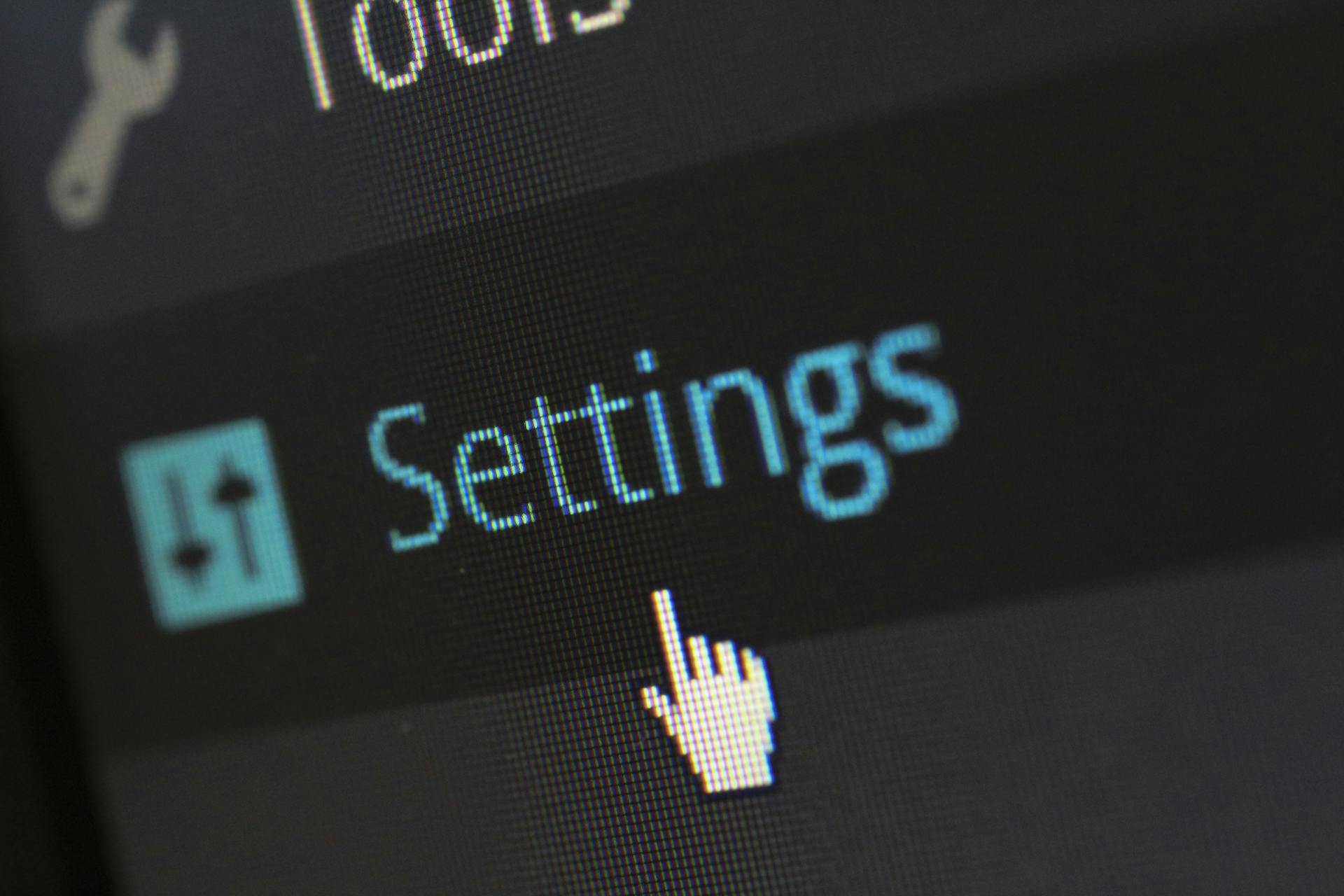
There are two main classes of computer numerical control (CNC) machine software: proprietary and open-source. Proprietary software is developed by companies that sell CNC machines, while open-source software is created by a community of developers who share their code freely. Some examples of popular proprietary CNC machine software include Mastercam, SolidWorks, and Catia. Open-source options include LinuxCNC, GRBL, and FreeCAD. Understanding the differences between these types of software can help you choose the best option for your needs.
A different take: Software Controls
1. Computer-Aided Design (CAD)
CAD, or computer-aided design, involves the use of CAD software to create 2D and 3D shapes or vector-based drawings of final products. Surface modeling CAD software offers additional features commonly used in designing common elements like evaluating mass properties and adding cable routing to the final part. With CAD, designers can create precise designs and models, which can then be used in CNC machining to produce the final product.
2. Computer Aided Manufacturing (CAM)
Computer Aided Manufacturing (CAM) refers to using cam software programs to control numerical control machine tools that are used in manufacturing. CAM programs matches cnc software embedded language and modern cam software programs include additional features like collecting feedback data to identify problems and improve production rate, reducing the need for human labor.
3. Computer-Aided Engineering (CAE)
Computer-Aided Engineering (CAE) is a software that is used to design and develop complex engineering products. It helps manufacturers to visualize the thermal properties, strength, and stress of their products before they are built. With CAE software programs and CAD software, parts manufacturers can simulate mechanical properties and ensure that their products meet the required safety standards.
How Does CNC Control Machine Tools Movement?
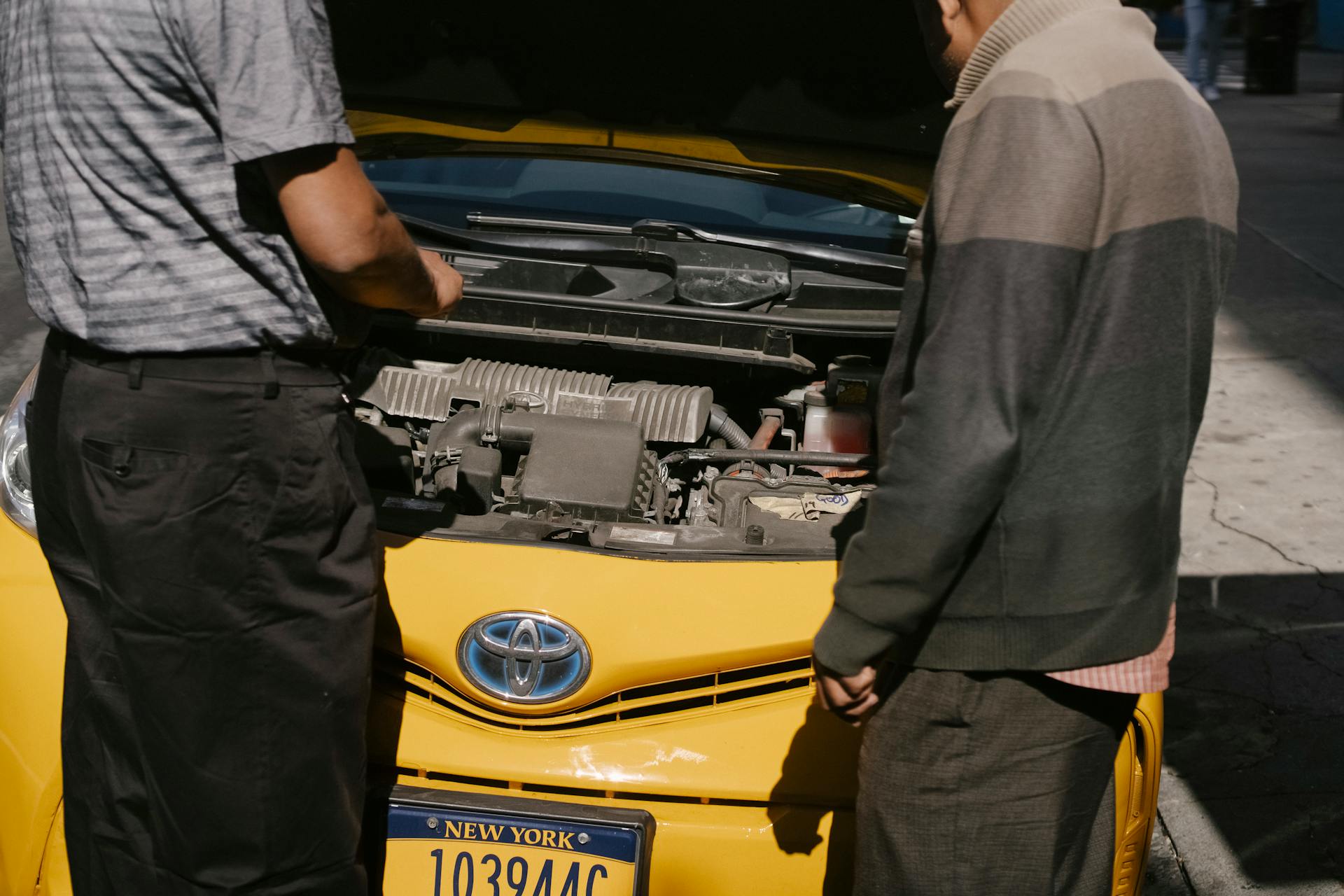
Computer numerical control (CNC) technology is a precise method of controlling machine tool movement. The positioning system used in CNC technology employs a rapid motion positioning and point interpolation method. This allows for faster production but requires careful programming due to the higher possibility of errors.
To move machine tools in a straight line or linear interpolation, the positioning method used is linear movement linear positioning. For diagonal movement, machine tools move parallel to each other in a controlled manner. The control system recalibrates the position of the machine tool at each step to ensure accuracy.
CNC technology also allows for circular positioning when moving round objects or hole punching. The circular positioning system moves in a round manner around the central axis of the object being worked on. With this level of precision, CNC technology has revolutionized manufacturing processes by providing accurate and efficient results that are not possible with traditional methods.
You might enjoy: Which of the following Is Important When Using Technology
1. Understanding the Machine Control Unit (MCU)
The machine control unit (MCU) is a small computer fitted to a CNC machine, which handles the movement and translation of the tool along with data processing. The control loop unit (CLU) collects feedback data from sensors on the machine, while the data processing unit (DPU) processes this information and sends it back to the MCU for movement software translation. By understanding how the machine control unit works, users can optimize their CNC machines for more precise operations.
Check this out: Internet Data Center
Discover the Range of Processes that Utilize CNC Systems
Computer numerical control (CNC) systems are used in numerous processes across multiple industries. The possibilities are endless with CNC systems, as they can be programmed to shape almost any material into virtually any shape or design. Some common CNC machining processes include milling, drilling, turning, and routing. Whether you're working in aerospace, automotive, or medical device manufacturing, chances are you're using computer numerical control to produce your products at a faster pace with greater precision than traditional methods.
1. CNC Milling
CNC milling is a process that removes material using a cutting tool and a rotary spindle. These rotating CNC systems, found in milling machines, have multi-axis capabilities such as 5-axis and 6-axis CNC mills. CNC milling machines work with metals, alloys, plastics, wood and are used in aerospace, military, and medical industries to make high-quality parts.
2. CNC Turning
CNC turning is a process in which a rotating workpiece is cut by a non-rotary cutting tool. As the workpiece rotates, cutting tools press against it to remove material and create circular or helical designs. CNC turning is commonly used for making shafts, cylinders, aluminum tubes, and pipe joints.
3. CNC Grinding
CNC grinding is a machining process where CNC grinders remove workpiece material using rotary abrasive wheels to add high precision and improve the workpiece surface. The edges CNC grinders create can remove sharp corners, making the finishing process much easier. This technology has become standard in many manufacturing industries due to its accuracy and efficiency.
Additional reading: How Can I Remove Dropbox from My Computer
4. CNC Electrical Discharge Machining (EDM)
CNC EDM machining processes remove material by using electrical pulses to erode metal materials. Electrode pulses create an electrical arc that removes material from the required location with high accuracy. CNC EDM is particularly useful for working with materials that conduct electricity, making it a valuable tool in precision manufacturing.
5. CNC Laser Cutting
CNC laser cutting is a highly precise and efficient method of removing material using a high-energy laser beam. The laser beam, which is an extremely high frequency light beam, can cut through materials as thin as a human hair. The CNC control system precisely moves the laser beam to create accurate cuts, making it an ideal choice for cutting non-metals alike. If you require cutting CNC laser is one of the most accurate cutting tools available.
6. CNC Waterjet Cutting
CNC waterjet cutting is an innovative process that uses high-pressure water to remove material from a variety of materials. The water pump pressurizes the water up to 90000 psi, allowing it to pierce metals, wood, glass, and alloys with high accuracy. This cold-cutting process is made possible by the cnc control system that handles the movement of the water nozzle, making it an efficient and accurate way to cut materials.
7. CNC Routing
CNC routing is a process that involves using a rotating blade controlled by a CNC machine to cut materials into precise shapes and sizes. The blade extends from the machine tool to provide straight cuts and intricate wood carvings, making it an essential tool for interior industries with complex designs. With its advanced technology, CNC routing capabilities are limitless, making it an exciting tool for those interested in precision cutting.
8. CNC Punching
CNC punching cuts a desired shape into materials like metal, plastic, or paper using machine tools. The process involves a punching die and can produce large volumes of consistent parts in circular, rectangular, and non-geometric angular shapes. Read on to learn more about how CNC technology is revolutionizing manufacturing.
9. CNC Plasma Cutting
CNC Plasma Cutting is a process that uses ionized gases to remove material from conductive materials such as copper, steel, and aluminum. This technology has become popular in metal fabrication shops and the automotive sectors due to its precision and efficiency in cutting metals. With CNC plasma cutting, businesses can create intricate designs with ease and accuracy.
10. CNC Welding
CNC welding combines manual welding technologies with the precision and control of CNC machines. By using a welding electrode and electrically conductive materials, strong welds are created with the required CNC welding specifications. This process eliminates labor requirements and ensures consistent, high-quality results.
11. 3D Printing
3D printing is a process that uses polymer filament to manufacture parts based on a required design. Unlike CNC machining controls, 3D printing is scalable in size and can be made in both small-scale workshops and large-scale manufacturing processes. The combination of CNC and 3D printing works well together, allowing for the manufacture of polymer parts with precision and accuracy.
Here's an interesting read: Computer Parts
Exploring the Difference Between NC and CNC Technology
NC and CNC machines are two different types of manufacturing methods. The numerical control machines use punch cards, requiring skilled operators to input alphanumeric data. On the other hand, computer numerical control machines use computer programs written in detailed coded instructions known as CNC code.
The main difference between NC and CNC technology is that errors occur more frequently with NC machine programs than with CNC programs. This is because NC machine codes cannot be easily edited once they have been punched into punch cards, while CNC codes can be considered significantly more flexible due to their ability to be edited on a computer. In conclusion, understanding the differences between these two technologies can help manufacturers choose the best method for their needs and ensure a smooth manufacturing process.
For another approach, see: How to Unsync Two Computers?
Frequently Asked Questions
What is Computer Numerical Control (CNC)?
Computer Numerical Control (CNC) is a manufacturing process that involves the use of computers to control and automate machines. This allows for precise and efficient production of complex parts and components.
What industries use computer numerical control systems?
Computer numerical control (CNC) systems are used in a variety of industries, including manufacturing, aerospace, automotive, and healthcare. These systems enable precise and efficient production of complex parts and components.
What materials can be CNC machined?
CNC machines can work with a variety of materials, including metals like aluminum and steel, plastics such as acrylic and PVC, and even wood. The material's hardness and durability will determine the type of cutting tool used during the process.
What are direct numeric controls?
Direct numeric controls are a type of control system that uses numerical values to adjust settings or operations. They are commonly used in industrial and manufacturing processes, allowing for precise and efficient control over machinery and equipment.
What is CNC and how does it work?
CNC (Computer Numerical Control) is a technology that allows machines to be controlled by computers. It works by converting digital design files into code that tells the machine what actions to take. This process enables precision and accuracy in manufacturing processes, making it an essential tool for modern industry.
Featured Images: pexels.com