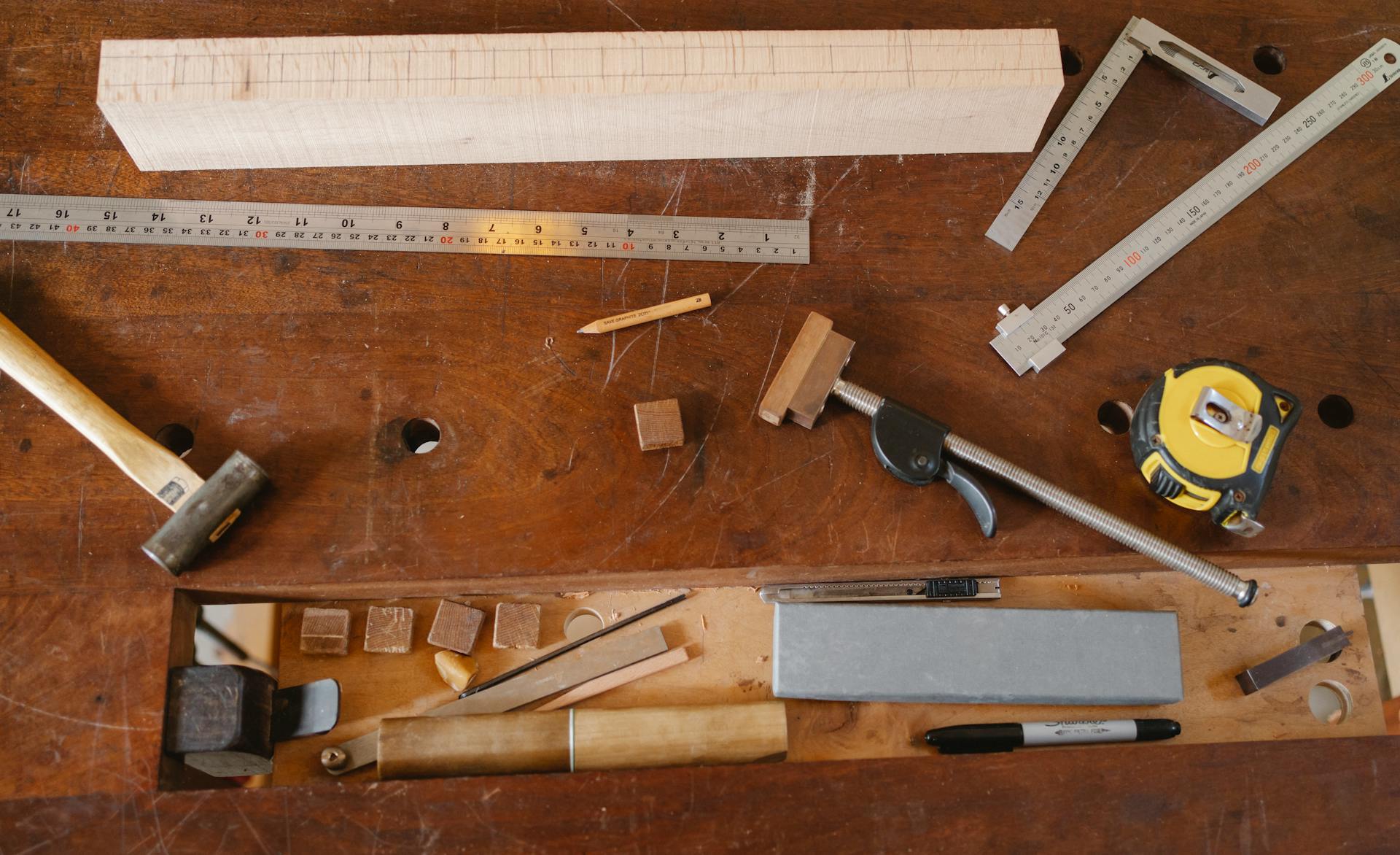
Calibration is a crucial aspect of any business, and its importance cannot be overstated. It's not just about ensuring accuracy, but also about maintaining a competitive edge.
Inaccurate measurements can lead to costly mistakes, such as overproduction or underproduction, which can result in significant financial losses.
A well-calibrated business can improve its profit margins by reducing errors and increasing efficiency.
By calibrating its equipment and processes, a business can ensure that its products meet the required standards, which can lead to increased customer satisfaction and loyalty.
Explore further: Why Are Leads Important
Importance of Calibration
Calibration is a crucial step in ensuring accurate measurements, and its importance cannot be overstated. Calibration is essential in the scientific laboratory because research is expensive and foundational to innovation, and non-accurate scientific measurement instruments can yield incorrect results and conclusions, causing expensive errors.
In chemistry, precise chemical amounts and environmental conditions are often required for successful product creation and delivery. If the scales on which you weigh ingredients are off by much, you probably know from personal experience that the outcome can be less than ideal.
A unique perspective: Why Is Accurate Data Collection Important
One of the main reasons calibration is important is to save money. Cost and waste reduction through standardization will increase profits. Calibration can also ensure safety, quality, and compliance to certifications.
A thermometer can drift due to exposure to extreme temperatures, and calibration can correct this drift error. Calibration provides traceability to national standards, if necessary, and increases consistency and reliability in products.
Calibration is a way to ensure measurements taken from a device are close to the true value. This is done by comparing the device output to a reference device that is more accurate. The calibration interval is usually found in the sensor's specification, but it's up to the user to determine when to re-calibrate based on experience with each sensor.
Here are the key benefits of calibration:
- Save money through cost and waste reduction
- Ensure safety and quality
- Ensure compliance to certifications
- Compensate for drift error
- Provide traceability to national standards
- Increase consistency and reliability
- Prevent and predict process failures
By calibrating equipment regularly, labs can ensure accurate results, extend the lifespan of their equipment, and maintain a safe working environment. Calibration is a crucial step in maintaining the accuracy and quality of measurements, and its importance cannot be overstated.
Calibration in Industry
In the pharmaceutical industry, calibration is crucial to ensure medications are effective and safe, with billions of people relying on it worldwide.
Many medications must be manufactured within tight temperature and humidity tolerances, and even a pipette measuring out drops of liquid in the manufacturing process is calibrated.
Calibration in manufacturing processes is also vital to prevent injury, death, and environmental disasters, as seen in cases where failure to calibrate or improper calibration has occurred.
In labs, calibration is done to ensure accuracy, longevity, and safety of equipment, which is a typical step in many industries.
Pharmaceutical
Calibration plays a crucial role in pharmaceutical manufacturing, ensuring that medications are effective and safe for consumption.
Many medications require precise temperature and humidity control to function properly, making calibration a vital step in the manufacturing process.
Even small variations in temperature and humidity can affect the efficacy and safety of medications, making calibration a critical factor in pharmaceutical production.
A pipette that measures out drops of liquid in a pharmaceutical manufacturing process is calibrated, demonstrating the importance of precision in this industry.
Calibration allows billions of people around the world to take medications with assurances of effectiveness and safety, making it a vital component in public health.
Suggestion: Making Folders and Filing Important Emails
Transportation
Calibration plays a crucial role in ensuring the safety and reliability of vehicles, which is especially important when you consider the thousands of pieces that make up a car, train, or plane.
The assurance of calibration is particularly relevant for aircraft, where a single malfunctioning bolt or rivet can have catastrophic consequences.
Billions of people rely on automobiles, trains, and planes for travel every day, making calibration a vital aspect of the transportation industry.
Without proper calibration, it's unsettling to think about the potential risks involved in traveling by air, with the possibility of bolts and rivets not meeting exacting metallurgical and mechanical specifications.
The calibration of test and measurement devices, manufacturing equipment, and guidance systems helps to mitigate these risks and ensure safe travel.
See what others are reading: Why Travel Insurance Is Important
Aerospace
The aerospace industry relies heavily on precise manufacturing and testing to ensure the safety and success of its products. Millions of pieces are assembled to produce planes, rockets, and satellites that need to perform as specified to avoid disaster.
Calibration is crucial in this industry to verify the accuracy of test and measurement devices. These devices are used in design, testing, and manufacturing to ensure that equipment and processes perform as specified.
The International Space Station is a prime example of why calibration is important. The temperature of space is about -270 degrees Celsius, which is very cold.
If the humid air inside the space station meets the cold window, ice would form and damage the space station. To prevent this problem, the windows are heated and monitored by a temperature sensor.
The temperature sensor is tested with a Fluke test and measurement device. This device is regularly calibrated by a calibrator, which is calibrated to the SI.
In contrast, companies that produce rocket fuel require high humidity to control static and reduce the possibility of explosion. This opposite requirement highlights the importance of calibration in ensuring that measurements are accurate and reliable.
Discover more: Performance Measurement Is Important Because
Manufacturing
In manufacturing, equipment used should be calibrated at multiple points across its working range to ensure reliable information to critical alarms and systems. This is crucial for preventing failures that can lead to injury, death, and even major environmental disasters.
Calibration is not just a precaution, it's a necessity in manufacturing. Failure to calibrate or improper calibration has been the cause of serious consequences in the past.
Manufacturers have a responsibility to ensure their equipment is calibrated correctly. This includes regular maintenance and calibration checks to prevent any issues from arising.
Lab Equipment Importance
Lab equipment calibration is crucial for accuracy, longevity, and safety in labs. This is because calibration ensures that instruments are functioning correctly, which is essential for reliable and repeatable measurements.
In manufacturing, equipment used should be calibrated at multiple points across its working range to ensure reliable information to critical alarms and systems. Failure to calibrate or improper calibration has been the cause of injury, death, and even major environmental disasters.
Calibration defines the accuracy and quality of measurements recorded using a piece of equipment. Over time, there is a tendency for results and accuracy to 'drift' when using particular technologies or measuring particular parameters such as temperature and humidity.
The goal of calibration is to minimize any measurement uncertainty by ensuring the accuracy of test equipment. Calibration quantifies and controls errors or uncertainties within measurement processes to an acceptable level.
Calibration is an ongoing process that requires maintenance throughout the lifetime of equipment to ensure reliable, accurate, and repeatable measurements.
A unique perspective: Why Is Accuracy Important
Temperature Carried Out
Calibration is often misunderstood as a single process, but it's actually two separate processes: calibration and adjustment. Calibration involves adjusting the output or indication on a measurement instrument to agree with the value of the applied standard, within a specified accuracy.
Understanding exactly what service you require is crucial, as different calibration methods suit different needs. For instance, a digital thermometer may be calibrated using a simulated temperature value, or a more rigorous method that reflects real-world usage.
A unique perspective: Why Is Customer Lifetime Value Important
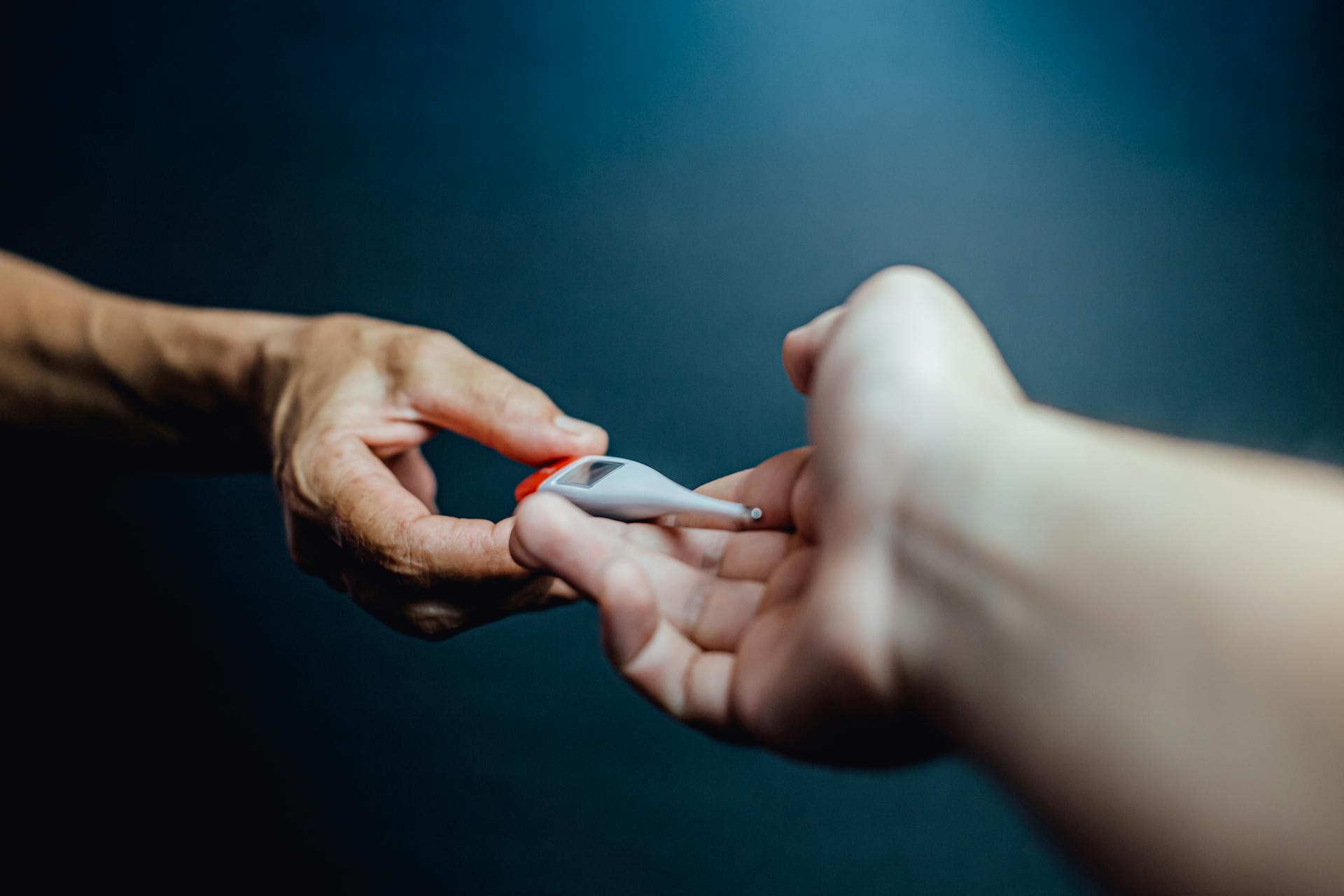
A simulated temperature value is applied to the thermometer only, without the temperature probe, and a test instrument is attached to record the result. This method is sufficient for some users, but others require a more comprehensive calibration.
In a system test, both the digital thermometer and the temperature probe are tested together, using a real heat source. The value displayed by the system is compared against the standard, which has a known or assigned accuracy.
It's essential to understand what is being calibrated and how the calibration is being performed to ensure accuracy and reliability.
A different take: Are the Most Important Part of an Information System
Calibration Frequency and Importance
Calibration is done annually for most industries, but the frequency can be adjusted based on results from calibration tests.
The cost of calibration is an investment that can help prevent the cost of incorrect readings.
You'll receive a printed calibration certificate as proof of quality standards after calibration, which you can retain for your records.
If this caught your attention, see: What Is an Important Factor That Help Determines Cost
Calibration Frequency
Calibration Frequency is an important consideration for any industry that relies on accurate measurements. The industry standard is to calibrate once a year.
This frequency allows businesses to have confidence in the results they monitor, record, and control. Calibration is a method for determining the best approximation of the true value of a measured quantity.
The results of calibration tests can help you adjust the frequency of calibrations as needed. Most calibration laboratories supply a printed calibration certificate to retain as proof of quality standards.
In fact, the standard is to calibrate annually for most industries. This frequency enables users and businesses to have confidence in the results that they monitor, record, and control.
Upgrading to more robust measuring instruments may be necessary based on the results of calibration tests. Most calibration facilities give customers a calibration tag and a printed calibration certificate to assure quality standards.
Additional reading: Why Is It Important to Support Local Businesses
Calibration Frequency for Instruments
The industry standard for most sectors is to calibrate instruments once a year. This frequency allows for regular checks and adjustments to ensure accuracy.
Manufacturers usually have a good idea of how long it will take for a sensor to drift to an out-of-tolerance condition, and they recommend a "calibration interval" based on this information. This interval can be found in the sensor's specification.
While the standard frequency is annual, the actual calibration interval may vary depending on the sensor's inherent calibration stability and the user's experience with each sensor. Some sensors may remain in tolerance longer than others.
Here's a general guideline for calibration frequencies:
Keep in mind that these are general guidelines, and the actual calibration frequency may need to be adjusted based on the specific requirements of your industry and equipment.
As you gain results from calibration tests, you can adjust the frequency of calibrations and upgrade to more robust measuring instruments if needed. Most calibration laboratories supply a printed calibration certificate for the customer to retain as proof of quality standards.
Safety and Compliance
Calibration improves safety by helping to maintain the proper environment for certain processes, especially those that are hypersensitive. Lithium-ion batteries, for example, must be produced in a place with less than 1% relative humidity to prevent the formation of dangerous byproduct chemicals.
Lab teams have to consider safety when calibrating their instruments, particularly for labs that deal with hazardous chemicals and solutions. Calibration accuracy is critical for quality work and the lab's safety.
By calibrating your equipment regularly, you may identify potential hazards and use them safely without risking damage or harm.
On a similar theme: Why Online Safety Is Important
Medical
Medical devices like pacemakers have a profound impact on millions of people worldwide, improving their quality of life and even saving lives.
A pacemaker made to exacting specifications with the help of test and measurement devices whose accuracy has been assured by calibration to the SI standard is crucial for its proper functioning.
Boston Scientific, a manufacturer of pacemakers, regularly calibrates their testing devices and manufacturing equipment with the best quality calibrators to ensure precise measurements and tests.
This is because a properly working and reliable pacemaker requires many precise measurements and tests, especially considering it connects directly to the heart.
Calibration provides the assurance that the manufacturing process meets specifications, which is critical for a pacemaker's functionality.
For example, a customer who received a pacemaker from Boston Scientific was in his early 30s before surgery, but was so ill that a short trip to the bathroom required a chair to rest on the way there and back.
After receiving the pacemaker, he felt a surge in energy and was able to enjoy normal activities like playing with his kids outside.
The significance of calibration cannot be overstated, as it ensures the accuracy of testing tools and manufacturing processes that affect millions of people with pacemakers.
Improves Safety
Calibration improves safety by helping to maintain the proper environment for certain processes, especially those that are hypersensitive. Lithium ion batteries, for example, require precise measurement and control to keep factory workers safe.
Lithium-ion batteries must be produced in a place with less than 1% relative humidity as lithium reacts easily with water vapor to form dangerous byproduct chemicals. This highlights the critical need for accurate measurements to prevent accidents.
Precision measurements assured by calibration in the manufacture of commercial airplanes is key to ensuring the safety of your next flight. Calibration is critical to the safe operation of commercial planes.
Lab teams have to consider safety when calibrating their instruments, particularly for labs that deal with hazardous chemicals and solutions. If lab equipment measurements or results are slightly off, it can put the entire lab and staff in danger.
By calibrating your equipment regularly, you may identify potential hazards and use them safely without risking damage or harm. Calibration helps organizations comply with government regulations, such as the FDA's requirements for precise chemical makeup of drugs.
A unique perspective: Important Safety Information for Iphone
What Are the Costs and Risks of Uncalibrated?
The costs of not calibrating can be catastrophic, including increased production costs due to manufacturing errors and false acceptance of non-compliant product.
In the US, defective products cause thousands of injuries every year, making personal injury a significant risk of not calibrating.
Product liability law makes it easier for injured people to recover damages, and manufacturers are held liable for defectively manufactured products that cause injury.
Liability doesn't stop with the manufacturer; all sellers in the distribution chain, including wholesalers and retailers, can be held accountable.
Manufacturers who don't use calibration to ensure safe production will be exposed to greater financial risk in court cases.
In fact, manufacturers may be required to defend their processes by showing calibration records, making it essential to maintain accurate records.
The costs of not calibrating can be avoided by investing in calibration, which can improve safety and save money by reducing false acceptance and rejection of products.
Recommended read: Why Are Medical Records Important
Accuracy and Reliability
Calibration is crucial for achieving accuracy in lab settings. Precise measurements and results are essential for any scientific lab, and instruments that haven't been calibrated can produce inaccurate results.
Lab workers rely on accurate instruments to produce reliable data, which is critical for research, testing, and quality control. Inaccurate results can lead to wasted time and resources.
Inaccurate instruments can make more mistakes until they're no longer worth using, which is why calibration is essential. Calibrating instruments helps eliminate data collection and analysis errors.
Consistent results are only possible when instruments are reliable and trustworthy, which is achieved through regular calibration. Regular calibration ensures that your instruments are reliable and trustworthy.
Calibration in Daily Life
Calibration plays a crucial role in our daily lives, often behind the scenes. We rely on accurate measurements and calibration to ensure the safety and reliability of various products and services.
Turning on a light or driving a car, for instance, depends on accurate R&D, measurements, and calibration to deliver the comfort and reliability we expect. Calibration of measurement instruments and other equipment to the SI impacts virtually all industries and most products we use.
Additional reading: When Storing Products It Is Important to
From taking medication to using a computer or phone, calibration is an essential part of the process. The image below illustrates the hidden ubiquity, importance, and role of calibration in our daily lives, by industry.
Calibration affects virtually all industries, including those related to our daily activities, such as healthcare, transportation, and technology.
Increase Profitability
Calibration helps increase profitability by saving money and cutting costs. This is achieved through standardization, which reduces waste and increases profits.
Cost reduction is a significant benefit of calibration. By standardizing processes and products, organizations can save money and boost their bottom line. In fact, calibration can help manufacturers and service providers produce quality products and services that get good customer reviews and loyal customers, ultimately leading to increased revenue.
Calibration also helps ensure safety by producing products and components that perform as expected and are safe to use. This is especially important in industries where safety is a top priority, such as healthcare and aerospace.
On a similar theme: What Is Most Important When Developing Easy to Use Products
Calibration can also help organizations shorten production time by providing quality components that are less likely to need replacement. This can be a significant time-saver, especially in high-volume production environments.
Here are some key benefits of calibration, summarized:
Ultimately, calibration is a worthwhile investment for any organization looking to increase profitability and improve overall performance.
Frequently Asked Questions
What is sensor calibration and why is it important?
Sensor calibration is the process of adjusting a sensor's output to match its input accurately, ensuring reliable and precise readings. Proper calibration is crucial in various fields, including science and industry, to maintain the dependability and accuracy of sensor data.
Why does calibration improve accuracy?
Calibration improves accuracy by compensating for the natural wear and tear of mechanical parts and electronic drift over time, ensuring the instrument operates as intended. Regular calibration helps maintain precise measurements and reliable results.
Sources
- https://www.fluke.com/en-us/learn/blog/calibration/why-is-calibration-important
- https://blog.mensor.com/blog/10-reasons-to-calibrate
- https://www.tempcon.co.uk/news/what_is_calibration
- https://conquerscientific.com/the-importance-of-calibrating-your-lab-equipment/
- https://nagman.com/blog/what-is-instrument-calibration-why-is-it-needed/
Featured Images: pexels.com