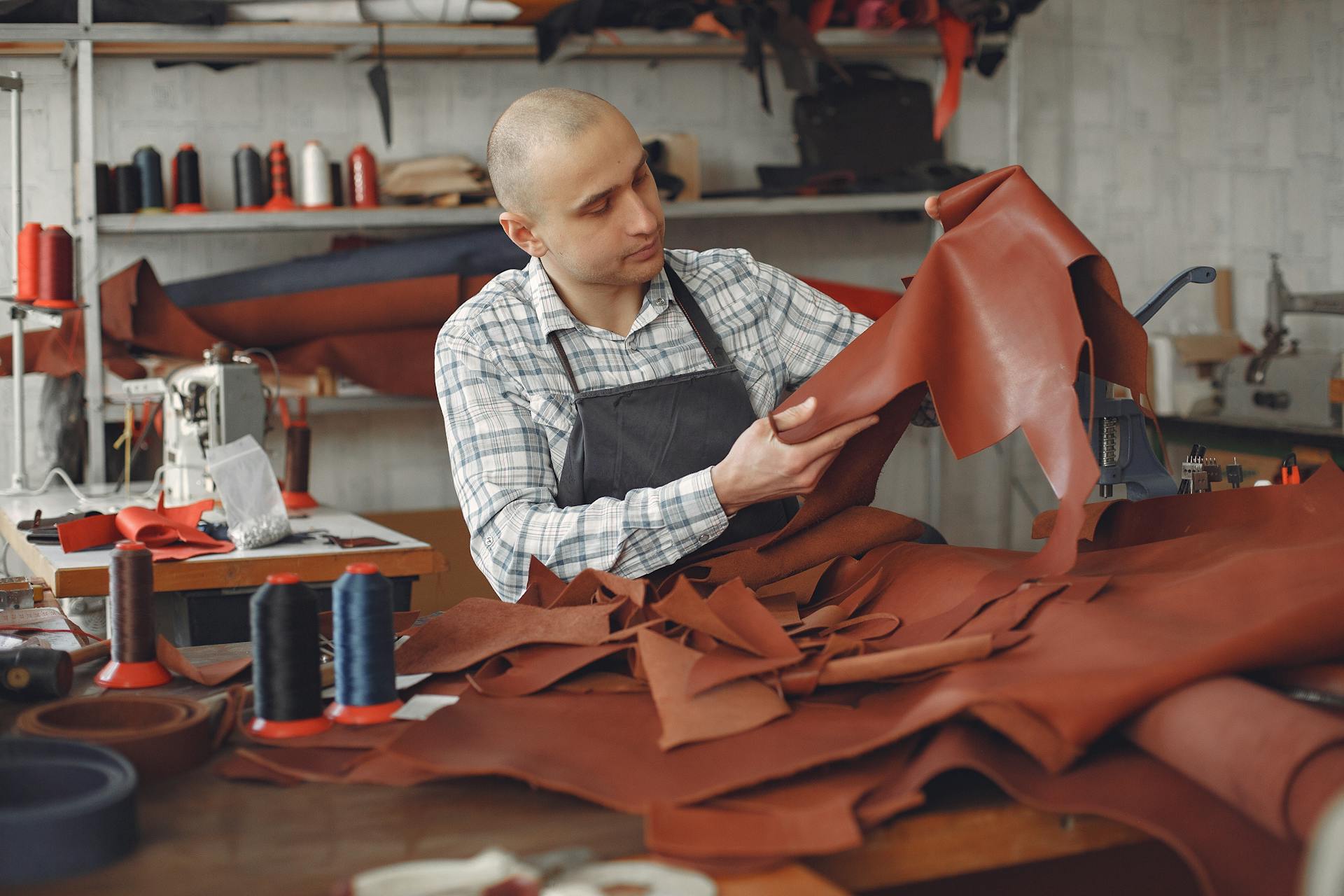
In today's market, quality assurance is crucial for businesses to stay competitive. A single mistake can lead to a loss of customer trust and revenue.
According to a study, 80% of consumers are more likely to do business with a company that has a reputation for quality. This highlights the importance of quality assurance in building customer loyalty.
With the rise of social media, negative reviews can spread quickly, damaging a company's reputation. A single negative review can deter up to 22% of potential customers from doing business with a company.
In the long run, investing in quality assurance can save businesses money by reducing the need for costly rework and repairs.
A unique perspective: Why Is It Important to Support Local Businesses
Why Quality Assurance Matters
Quality assurance is crucial for building a positive reputation. Errors and inconsistencies in products can damage your reputation and lead to unhappy or even lost customers.
Companies that prioritize quality assurance are more likely to retain customers. Preventing customer loss is a significant benefit of quality assurance, as it can be expensive to replace lost customers.
Quality assurance boosts customer confidence by showing that a company cares about its clients and their priorities. Companies known for their quality and consistency always do better with customers.
A fresh viewpoint: Most Important Companies in the World
Prevent Customer Loss
Preventing customer loss is a major benefit of quality assurance. In fact, errors and inconsistencies in products can damage your reputation and lead to unhappy or even lost customers.
If products are released with errors or don't align with what your clients are looking for, it's only a matter of time until your clients decide to switch to a competitor's product. Quality assurance helps to ensure that this doesn't happen.
Companies that use quality assurance processes are letting customers know that they care about them and their priorities. This helps to boost customer confidence and retain existing customers.
By preventing customer loss, quality assurance can also help you save money that would have been spent on acquiring new customers.
Intriguing read: What Is Most Important When Developing Easy to Use Products
What Is (QC)?
Quality control is a process that helps businesses ensure their products meet high standards. It involves creating an environment where employees strive for perfection through training and setting benchmarks for product quality.
By establishing well-defined controls, companies can standardize production and reactions to quality issues. This limits room for error and reduces the chance that employees will be involved in tasks for which they're not adequately trained.
Quality control requires testing products to check for statistically significant variations. This ensures that products meet the desired quality standards.
You might enjoy: When Storing Products It Is Important to
Benefits of Quality Assurance
Quality assurance is essential for any business, and its benefits are numerous. It's a vital part of building a great reputation, which boosts customer confidence and loyalty. A good reputation is vital for all stakeholders, including investors and suppliers.
Quality assurance helps prevent errors and inconsistencies in products, leading to positive reputation, satisfied customers, and new clients. This is achieved through quality assurance services that allow preventing errors and mistakes from happening.
By releasing high-quality products, businesses can prevent customer loss. In fact, if products are released with errors or don't align with what clients are looking for, it's only a matter of time until clients decide to switch to a competitor's product.
A different take: When Communicating It's Important to
Quality assurance also saves time and money. Fixing errors in the production stage can take up to 150 times longer than repairing them earlier in the requirements design stage. This is a significant advantage for businesses that want to be efficient and cost-effective.
In addition, quality assurance has a positive impact on employee morale. When employees understand what's expected of them, they are less stressed and better able to focus on meeting established standards.
Quality assurance also leads to more long-term profit. By saving money and time, businesses can be more competitive in the marketplace. Loyal stakeholders will hype up a business, which translates into more sales and long-term profit.
Here are some key benefits of quality assurance:
- Boosts customer confidence and loyalty
- Prevents errors and inconsistencies in products
- Saves time and money
- Prevents customer loss
- Has a positive impact on employee morale
- Leads to more long-term profit
Quality assurance is a vital part of any business, and its benefits are numerous. By implementing quality assurance processes, businesses can ensure that their products and services meet the needs and expectations of their customers.
Additional reading: What Is Software Quality Assurance and Why It Is Important
Quality Assurance in Business
Quality assurance is the foundation of a business' work culture, setting the tone for the whole organization. It's a drive for quality that infuses every part of the business, and everyone has a role to play.
Anything that seems to be inhibiting the organization's ability to provide quality to their customers is addressed. A work culture focused on meeting certain standards is good for everyone - stakeholders, employees, and the business itself.
Data quality is essential for providing customers with the best possible experience. A single bug can have a ripple effect that impacts the entire company.
Companies must monitor data quality, identify any issues that could be affecting it, and make sure the data is suitable for the purpose it was collected for. When data does not meet the expected standards, it can adversely affect customer service, employee productivity, and business strategies.
Here are some key aspects of a quality assurance plan:
- Functional testing
- Non-functional testing
- User acceptance testing
- Performance testing
- Security testing
- Compatibility testing
Quality assurance and testing help to avoid costly mistakes by catching errors and problems before they can cause any damage. This minimizes the need for reworking or fixing them later on.
The quality assurance process is all about consistently maintaining high standards. Many of those standards depend on what customers ask for, and businesses committed to quality will listen and use those suggestions to perfect and upgrade their offering. This keeps customers happy and loyal to the business.
Quality Assurance Methods
Quality assurance utilizes one of three methods. These methods help ensure that products meet defined business requirements.
There are several methods quality control uses to communicate and track inspections and issues. A quality control chart is a graphic that depicts whether sampled products or processes are meeting their intended specifications.
Quality assurance is more focused around processes and procedures, while testing is focused on the logistics of using a product in order to find defects. Quality assurance defines the standards around testing to ensure that a product meets defined business requirements.
Quality control charts come in two main types: univariate and multivariate charts. A univariate chart analyzes a specific product attribute, while a multivariate chart measures variances in several product attributes.
A unique perspective: Why Is Product Management Important
Statistical Process
Statistical process control (SPC) is a methodology based on objective data and analysis. It was developed by Walter Shewhart at Western Electric Company and Bell Telephone Laboratories in the 1920s and 1930s. SPC uses statistical methods to manage and control the production of products.
Curious to learn more? Check out: Why Is Statistical Significance Important
SPC is a powerful tool for identifying and addressing quality issues early on in the production process. By using statistical methods, SPC can help manufacturers to detect and correct problems before they become major issues.
Here are some key benefits of using SPC:
- Early detection of quality issues: SPC can help manufacturers to identify quality issues early on in the production process, reducing the risk of costly rework or recalls.
- Improved process control: SPC can help manufacturers to better understand and control their production processes, leading to improved product quality and reduced variability.
- Reduced waste: SPC can help manufacturers to reduce waste by identifying and addressing quality issues early on in the production process.
To implement SPC, manufacturers can use a variety of tools and techniques, including:
- Control charts: Control charts are a type of statistical chart that can be used to monitor and control production processes.
- Process capability analysis: Process capability analysis is a statistical technique that can be used to determine whether a production process is capable of producing products that meet customer requirements.
- Root cause analysis: Root cause analysis is a statistical technique that can be used to identify the underlying causes of quality issues.
By using SPC, manufacturers can improve the quality of their products, reduce waste, and improve their overall efficiency and effectiveness.
What Are 3 Examples?
In the food industry, quality control is crucial to ensure the safety and quality of the products. Overseeing the ingredient specifications is a vital aspect of this process.
Reviewing supplier lists is another important step to guarantee the quality of the ingredients. This involves verifying the suppliers' credentials and ensuring they meet the required standards.
Ensuring the facility where the food product is made is sanitary is essential for preventing contamination and maintaining a clean environment.
Quality Assurance in Industry
Quality Assurance in Industry is crucial because creating a product is costly and time-consuming without controls in place. This can lead to defective or unsafe products being sent out for purchase.
Companies that send out defective products can be held liable for injuries or issues that arise from using their products. This can result in financial losses, damage to their reputation, and even lawsuits.
Quality control inspectors play a vital role in identifying defective or unsafe products and correcting their causes. By doing so, they help prevent injuries, save lives, and ensure that products meet the required standards.
QC by Industry
Quality control varies significantly across different industries. In food and drug manufacturing, chemical and microbiological testing of samples is crucial to ensure consumer safety.
Companies in this sector must perform rigorous testing to prevent harm to consumers. This includes verifying that products meet strict standards for purity and potency.
In aircraft manufacturing, documentation, tracking, inspecting, and re-inspecting all items and phases of a build is essential. This ensures that every component meets the highest standards of quality.
Automobile manufacturers focus on ensuring parts meet specifications and tolerances. This includes verifying that engines, drive trains, and other mechanical parts operate smoothly and efficiently.
Quality testing in electronics might involve using meters to measure the flow of electricity and stress testing to identify potential issues.
For your interest: Why Are Standards Important for Protocols
Uses by Industry
Quality assurance is a vital process in various industries, ensuring that products meet specific requirements and are free from defects. Manufacturers take the lead in formalizing the quality assurance discipline.
In the manufacturing industry, QA is crucial to ensure assembled products meet product specifications and requirements. This is a must-have process to maintain customer trust and satisfaction.
Manufacturers use quality assurance to detect and eliminate defects in their products. For instance, food production uses X-ray systems to detect physical contaminants in the food production process.
Food production is a high-risk industry where contaminants can have serious consequences. X-ray systems help identify and remove contaminants before products leave the factory.
Pharmaceutical companies also employ quality assurance to ensure drug development meets strict standards. QA processes include reviewing documents, approving equipment calibration, and investigating market returns.
Pharmaceutical companies take QA very seriously, as the consequences of a failed product can be severe. This includes reviewing training records and manufacturing records to ensure compliance.
Here are some examples of industries that use quality assurance:
- Manufacturing
- Food production
- Pharmaceutical
Quality Assurance Tools and Software
Implementing quality assurance (QA) tools and software is crucial for ensuring the quality of software development. These tools automate and orchestrate testing to facilitate QA goals.
Selenium is an open-source software testing program that can run tests in various popular software languages, such as C#, Java, and Python. This makes it a versatile option for developers.
Jenkins is another open-source program that enables developers and QA staff to run and test code in real-time. It's particularly well-suited for fast-paced environments, automating tasks related to building and testing software.
Postman is a tool used for web apps or application program interfaces (APIs), automating and running tests. It's available for Mac, Windows, and Linux, and supports Swagger and RAML formatting.
To choose the right QA tools and software, consider the specific needs of your project and the advantages of each approach. For example, Selenium is great for cross-language testing, while Jenkins excels in real-time testing.
Here are some popular QA tools and software, along with their key features:
- Selenium: Open-source software testing program for cross-language testing
- Jenkins: Open-source program for real-time testing and automation
- Postman: Tool for automating and running tests on web apps and APIs
Career and Education
To pursue a career in quality control, you'll typically need a high school diploma for entry-level positions, although a bachelor's degree may be required depending on the industry.
You'll also need experience in the industry, and in some cases, licenses and certifications. This can vary depending on the specific industry or business you're working with.
To succeed in quality control, you'll need a combination of skills, including attention to detail, mechanical and math skills, physical abilities and strength, technical skills, and the ability to perform under pressure.
Careers
If you're looking for a career that's all about making products better and safer, quality control might be the way to go. To become a quality control inspector, you'll typically need a high school diploma for entry-level positions.
A bachelor's degree may be required depending on the industry, and experience in that industry is also a must. Some industries and businesses may also require licenses and certifications.
Attention to detail is crucial for quality control professionals, as is having mechanical and math skills. Physical abilities and strength are also necessary for some roles.
For more insights, see: The Most Important Aspect S of a Company's Business Strategy
Salaries
Salaries for quality control professionals vary depending on the industry and experience level. The average pay is around $48,680 in professional, scientific and technical services.
As you gain more experience, your salary will likely increase. In fact, the Bureau of Labor Statistics reports that the average salary for quality control inspectors is higher in certain industries.
Here are some average salary ranges for quality control professionals in different industries, according to the Bureau of Labor Statistics:
These figures can help you plan your career and education goals. Remember to consider your experience and industry when evaluating salary ranges.
Frequently Asked Questions
What is the main point of quality assurance?
The main point of quality assurance is to boost a company's credibility and competitiveness. It achieves this by improving work processes and efficiency.
What is the most important aspect of quality assurance?
The core of quality assurance is establishing a culture of accountability that drives continuous improvement and product integrity. This is achieved by setting quality objectives, measuring results, and maintaining rigorous standards and processes.
Why is quality testing important?
Quality testing is crucial for protecting a brand's image and maintaining customer trust by ensuring consistent, high-quality products. It's a key factor in building a strong reputation and long-term customer loyalty.
Sources
- https://geeksforless.com/quality-assurance-why-its-a-must-for-your-business/
- https://theimportantsite.com/10-reasons-why-quality-assurance-is-important/
- https://www.techtarget.com/searchsoftwarequality/definition/quality-assurance
- https://www.investopedia.com/terms/q/quality-control.asp
- https://www.turing.com/blog/software-quality-assurance-and-its-importance
Featured Images: pexels.com