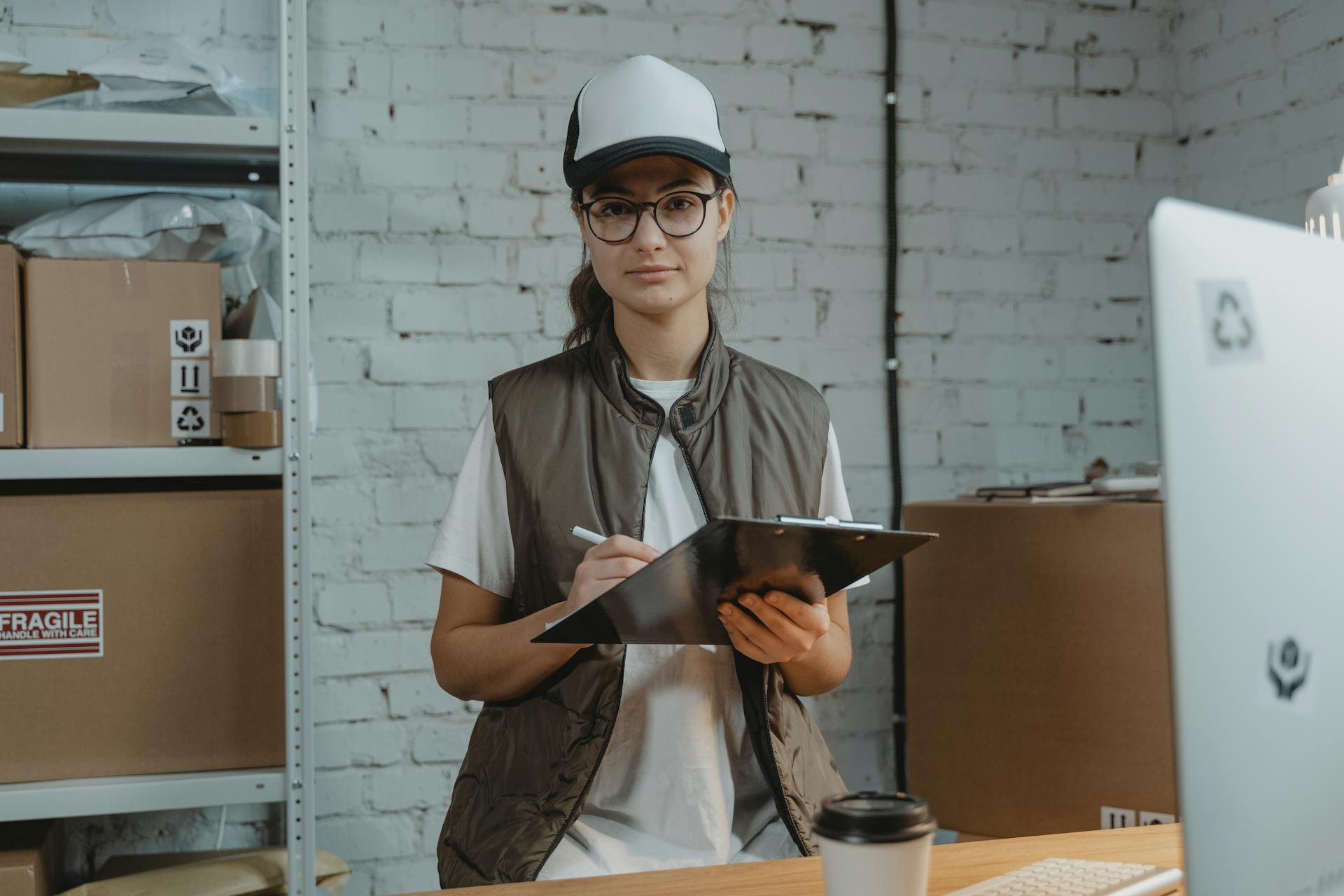
Quality management is a crucial aspect of any business, and its importance cannot be overstated. By implementing a quality management system, organizations can significantly reduce waste and rework, which can account for up to 25% of production costs.
Effective quality management also leads to increased customer satisfaction, as it ensures that products meet customer expectations and needs. This, in turn, can lead to repeat business and positive word-of-mouth, which can be a powerful marketing tool.
In addition to these benefits, quality management can also help organizations reduce costs associated with defects and errors, which can be as high as 20% of production costs. By identifying and addressing quality issues early on, organizations can prevent costly problems down the line.
Benefits of Quality Management
Implementing quality management can lead to significant cost savings, as seen in the case of Toyota, which reduced its defect rate by 90% after implementing the Total Quality Control (TQC) program.
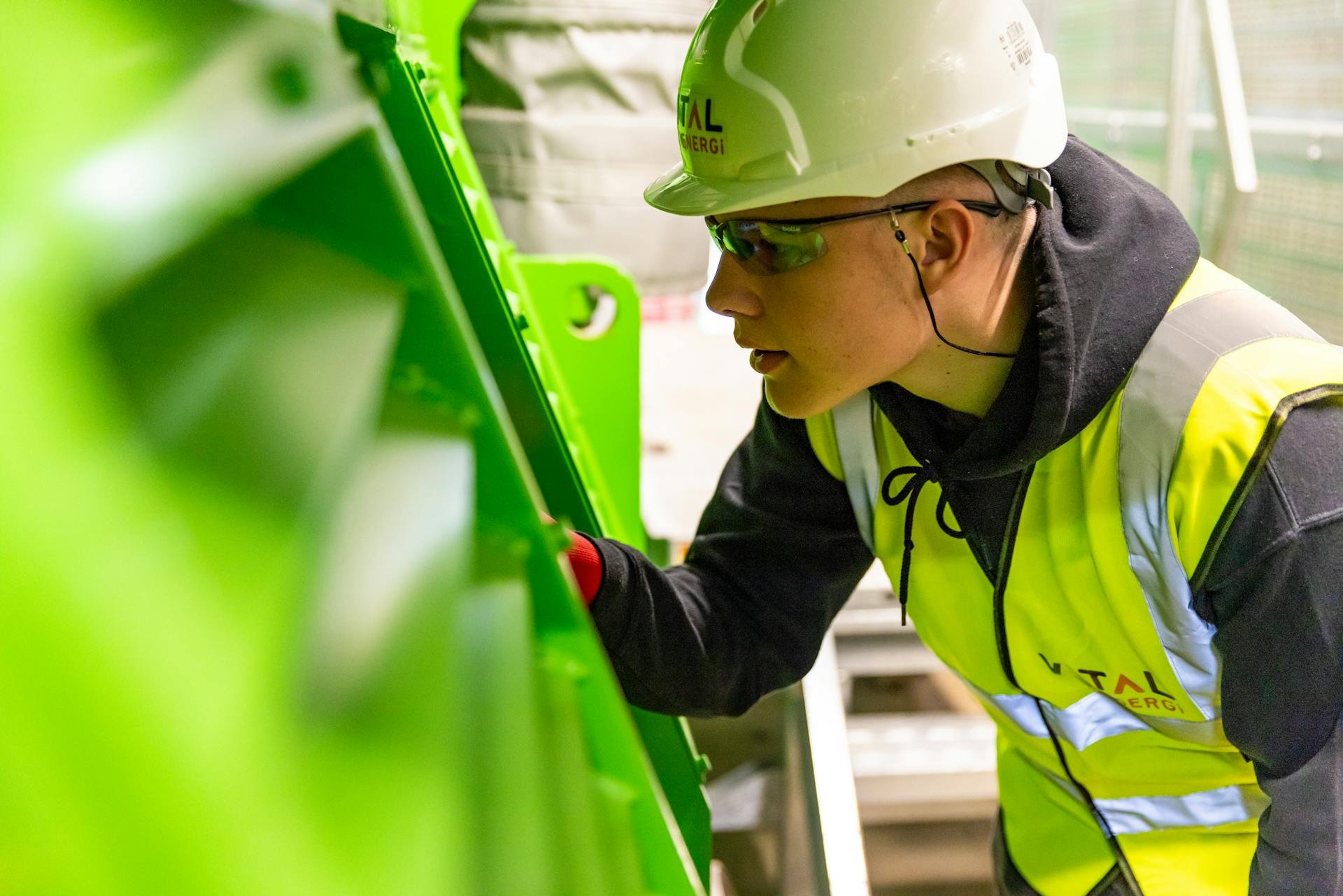
By reducing waste and defects, quality management can increase efficiency and productivity, allowing companies to produce more with less resources.
Studies have shown that companies with robust quality management systems experience a 20% increase in customer satisfaction.
Quality management also helps to reduce the risk of product recalls, which can be costly and damage a company's reputation.
Effective quality management can lead to improved employee morale, as seen in the case of companies that prioritize employee training and development.
Companies that prioritize quality management tend to experience higher profits, with some studies showing a 10% increase in revenue.
By focusing on quality, companies can build trust with their customers and establish a strong reputation in the market.
For more insights, see: Why Is Candidate Experience Important
Operational Efficiency
Operational efficiency is a crucial aspect of any business. Ensuring long-lasting efficiency is not only limited to staff working in manufacturing, but also extends to every employee and machinery within the firm.
A Quality Management System (QMS) helps in streamlining business processes, making it easier to identify issues and problems inherent in processes. This structured approach strengthens overall business processes.
You might like: Efficiency and Effectiveness Are Most Important for
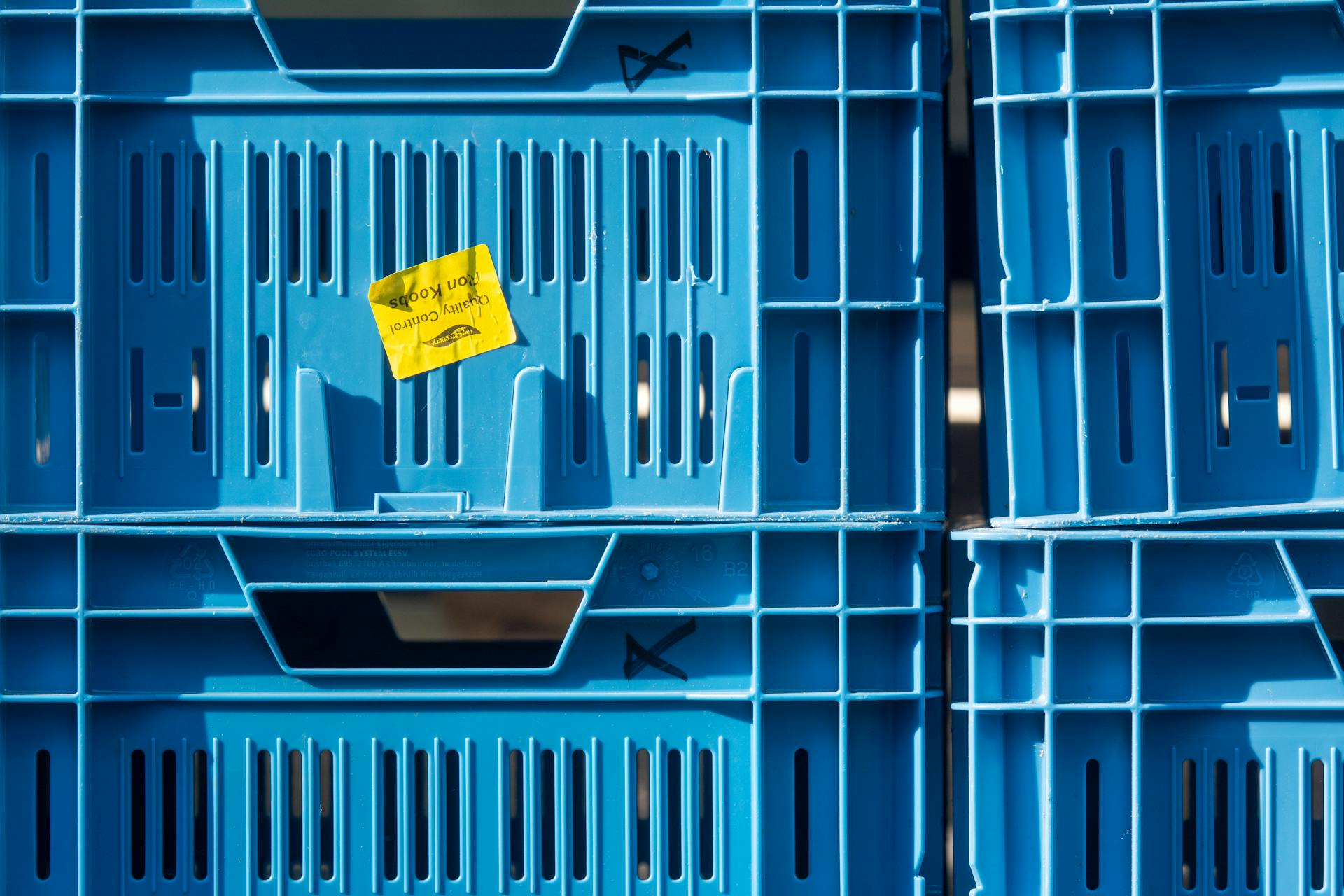
By understanding and following the importance of Quality Management, employees gain confidence and agility, which elevates their efficiency in manifold ways. This, in turn, has a cascading effect on the overall sales and profits of the firm.
A QMS is an investment in a company's future, built-in efficiency helps in reducing costs and time involved in delivering products and services. This results in more profit for the business and happier customers who receive their orders more efficiently.
Streamlining business processes helps in responding to market demands quickly and efficiently, making it a necessity in any business.
Curious to learn more? Check out: Why Is Efficiency Important
Customer Satisfaction and Loyalty
Customer satisfaction is directly linked to quality management, as it ensures a higher level of customer satisfaction and happiness.
In today's market, customers are presented with many options and alternatives, and they're more aware of quality standards thanks to social media and digital marketing.
To retain loyal customers, businesses must follow the importance of quality management, as it's a crucial factor in attracting and retaining customers.
Take a look at this: The Most Important Aspect S of a Company's Business Strategy
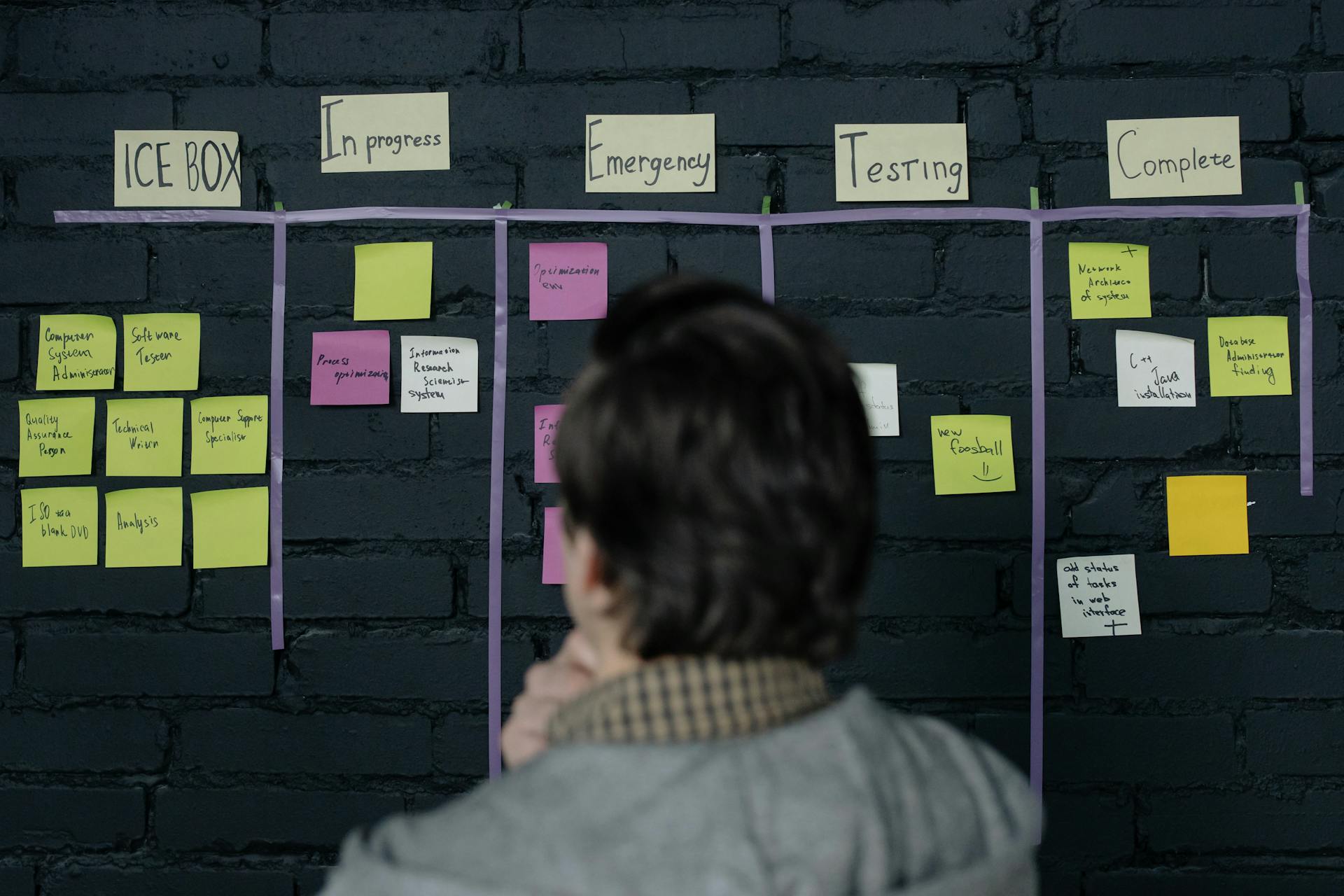
Customers are willing to pay extra for high-quality products, and any glitches in quality can quickly damage a brand's reputation.
With the power of social media, negative experiences can spread quickly and make it viral, deteriorating the brand value of the firm.
In a competitive market, businesses can only survive and thrive if they're able to retain a loyal set of customers, which is only possible through quality management.
Competitive Advantage
In today's competitive market, beating the competition is crucial for survival and success. This can be achieved by understanding the importance of quality management and making it a core part of a company's objectives and work culture.
Many brands have had to shut down stores and operations due to their inability to adhere to quality standards. This highlights the need for quality management to stay ahead in the market.
To beat the competition, firms need to follow a set of guidelines and principles for each business operation, starting from top management to management trainees. This ensures everyone is on the same page.
Check this out: Most Important Metrics Builders Need to Keep Track of
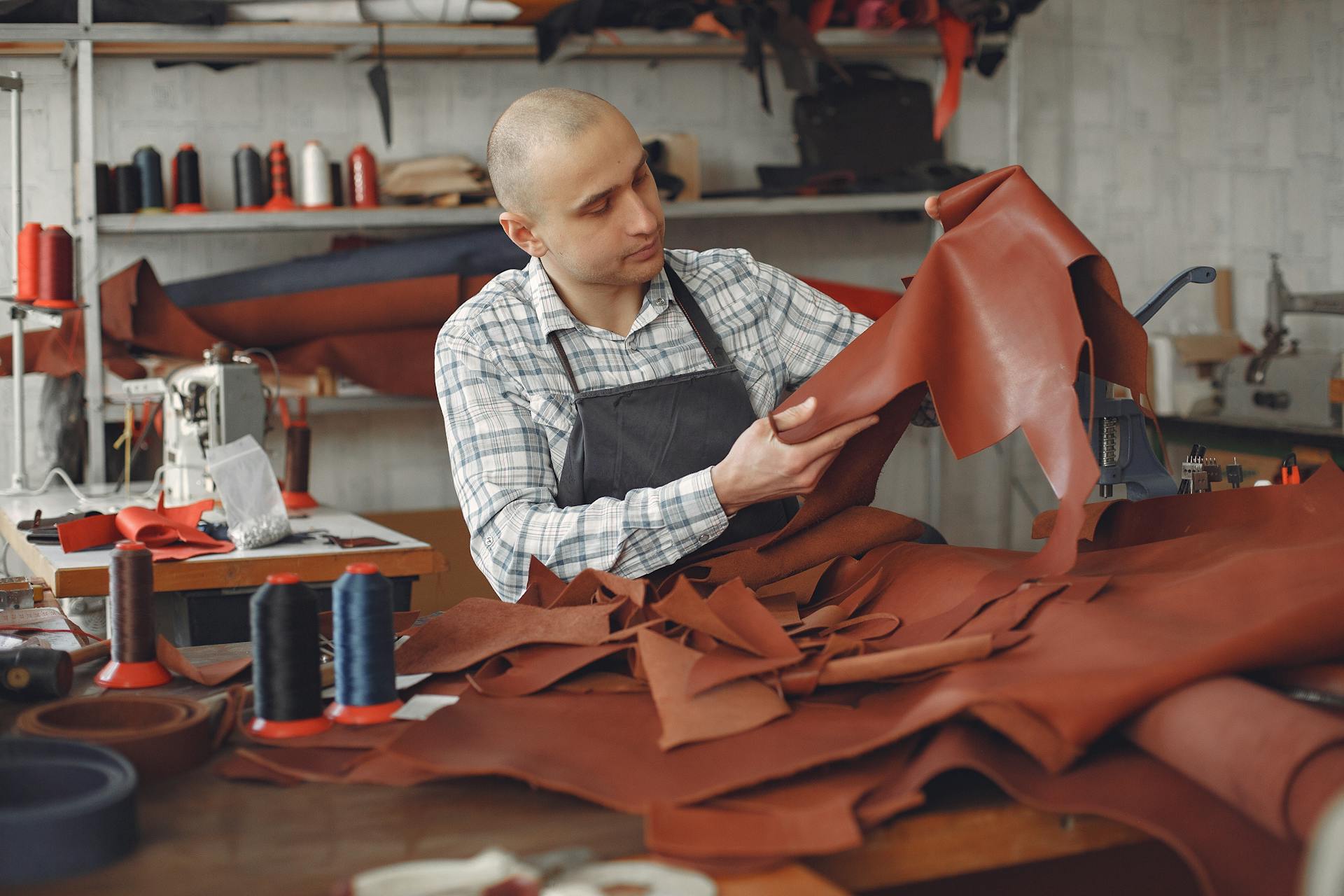
Firms that follow quality management principles can carve a distinctive identity for their brand in the market. This sets them apart from competitors and helps build a loyal customer base.
By prioritizing quality management, companies can enhance their brand value and equity. This, in turn, leads to a higher market share and increased revenue.
Risk Management
Risk Management is crucial for any business to maintain its brand value. Risks occur in business operations when quality parameters are not adhered to.
Risk mainly occurs during the manufacturing process of the products. This is a vital aspect of the business where quality management is essential.
By understanding the importance of quality management, firms can minimize risks and ensure smooth business operations.
If this caught your attention, see: Why Is Operations Important
Qms Helps Meet Auditor Requirements
A quality management system (QMS) is a game-changer when it comes to meeting auditor requirements. With a QMS in place, you can make the process of meeting these requirements much easier.
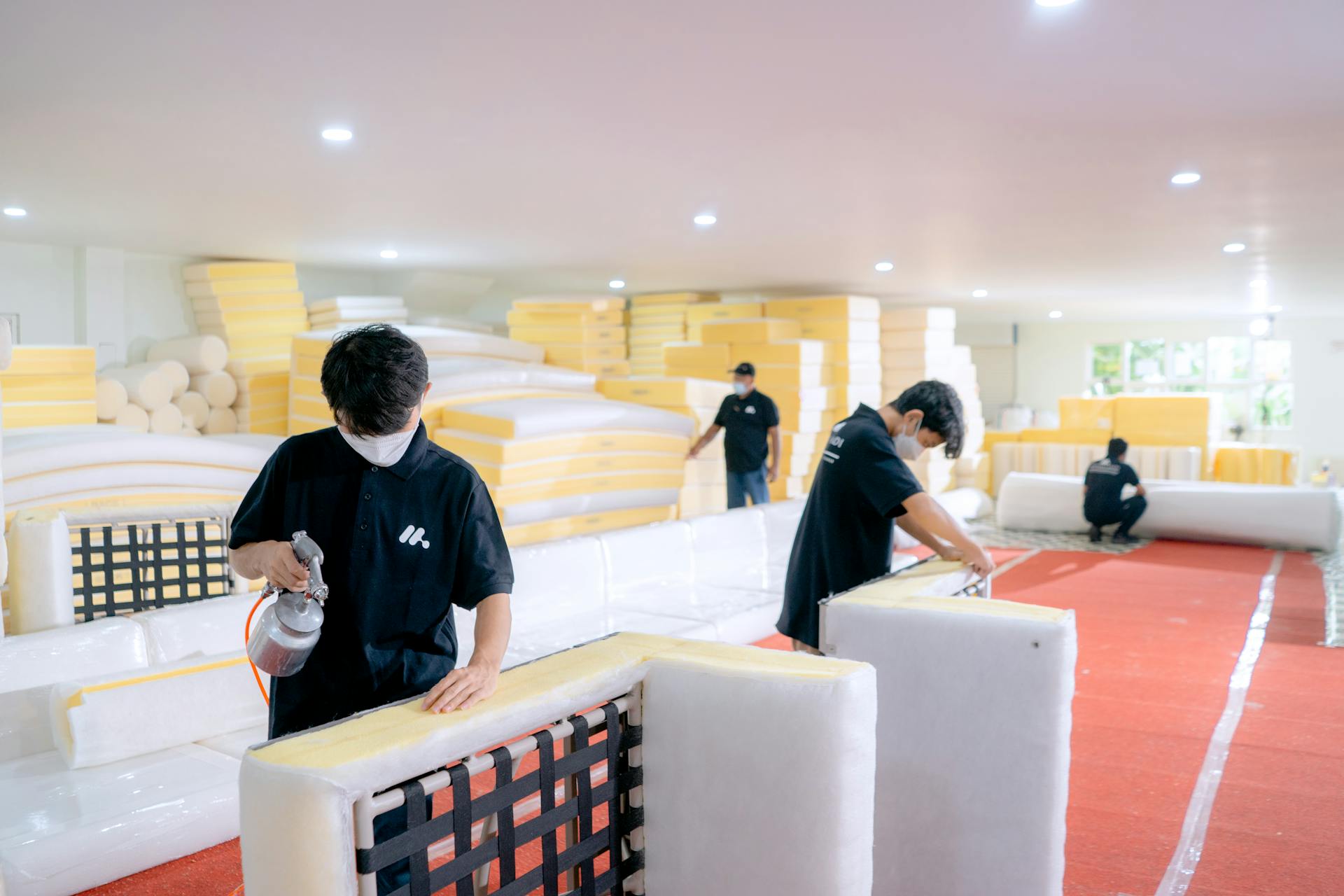
Having a documented QMS means you have a clear and detailed record of the steps required to meet the necessary standards, and what is required to maintain them. This makes it easy to show auditors that your company and your team are meeting all necessary requirements.
Meeting auditor requirements can be difficult and costly without a QMS, but with one in place, you can save time and money while increasing efficiency and avoiding costly rework. A QMS can help you detect problems before they happen, reduce costs and waste, and streamline your business processes.
A different take: An Important Update Is Required for Woocommerce
Reduced Risks
Reducing risks is a vital aspect of any business operation, and a Quality Management System (QMS) can help achieve this.
Risks mainly occur during the manufacturing process and while dealing with customers during before and after sales procedures.
A QMS is essentially a risk management system that allows you to analyze your processes and identify areas of risk.
A fresh viewpoint: Important Interview Questions to Ask
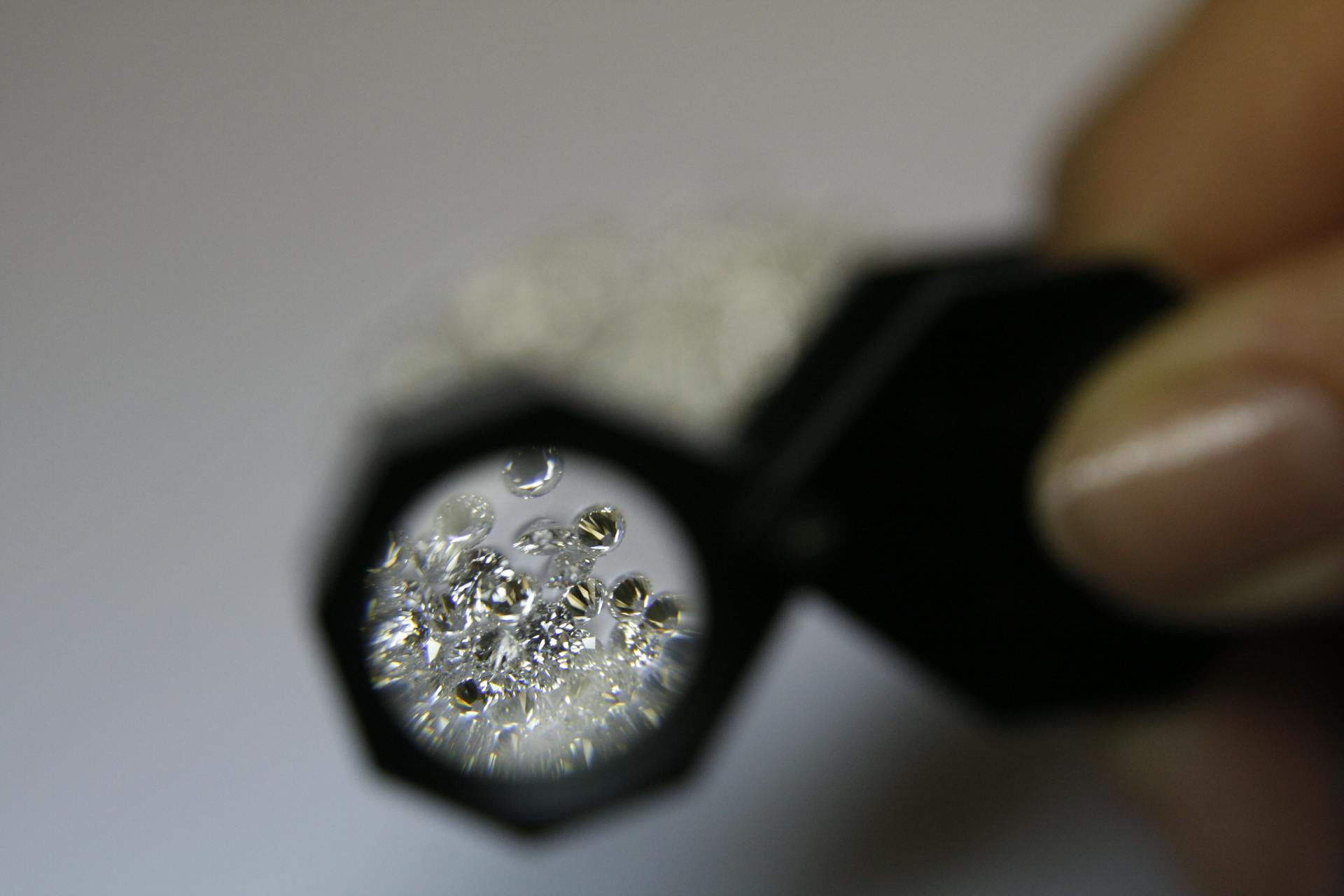
By identifying issues in your production or service delivery processes, you can address them before they affect your customers, reducing the risk of lost sales and complaints.
Any problems caught early on can be logged and addressed, preventing them from turning into major issues that negatively affect your bottom line.
A QMS can help you detect problems before they happen, making it a valuable investment in your company's future.
Carefully examining every step in your processes can help you reduce costs and time involved in delivering your product and services, as well as the waste that goes along with these activities.
Related reading: What Is an Important Factor That Help Determines Cost
Financial Benefits
Implementing a quality management system (QMS) can significantly reduce costs and waste by streamlining processes and eliminating inefficiencies.
A QMS helps you identify areas of risk, allowing you to address problems before they affect your customers and reduce the risk of lost sales and complaints.
By examining every step in your processes and devising ways to streamline them, you can reduce costs, time, and waste involved in delivering your product and services.
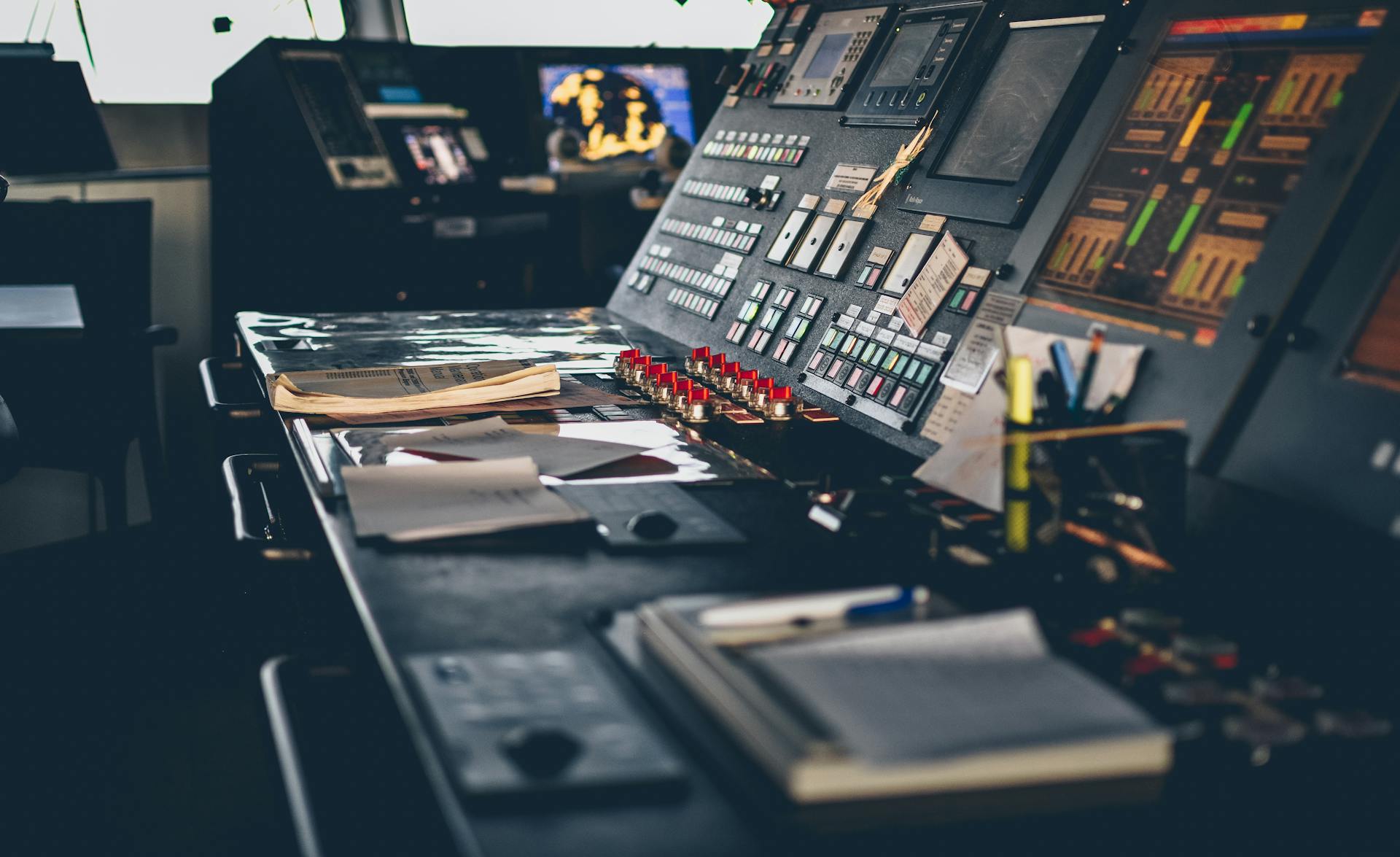
This, in turn, leads to more profit for your business and happier customers who receive their orders more efficiently.
A QMS also helps you catch smaller problem areas earlier, preventing them from causing major issues that negatively affect your bottom line.
This can result in increased revenues and profits, ensuring a high level of customer satisfaction, high brand value, and a competitive edge.
Qms Reduces Costs and Waste
Implementing a Quality Management System (QMS) can have a significant impact on reducing costs and waste in your business. A QMS is a long-term investment that pays off by streamlining processes and increasing efficiency.
By examining every step in your processes and finding ways to improve them, you can reduce the time and resources involved in delivering your product and services. This means more profit for your business.
A QMS helps you identify issues and problems in your processes, which can be causing problems and bottlenecks. By addressing these issues, you can strengthen your overall business processes.
With a QMS, you can respond quickly and efficiently to market demands, which is crucial in today's fast-paced business environment. This is made possible by streamlining your systems and processes.
Increased Revenues and Profits
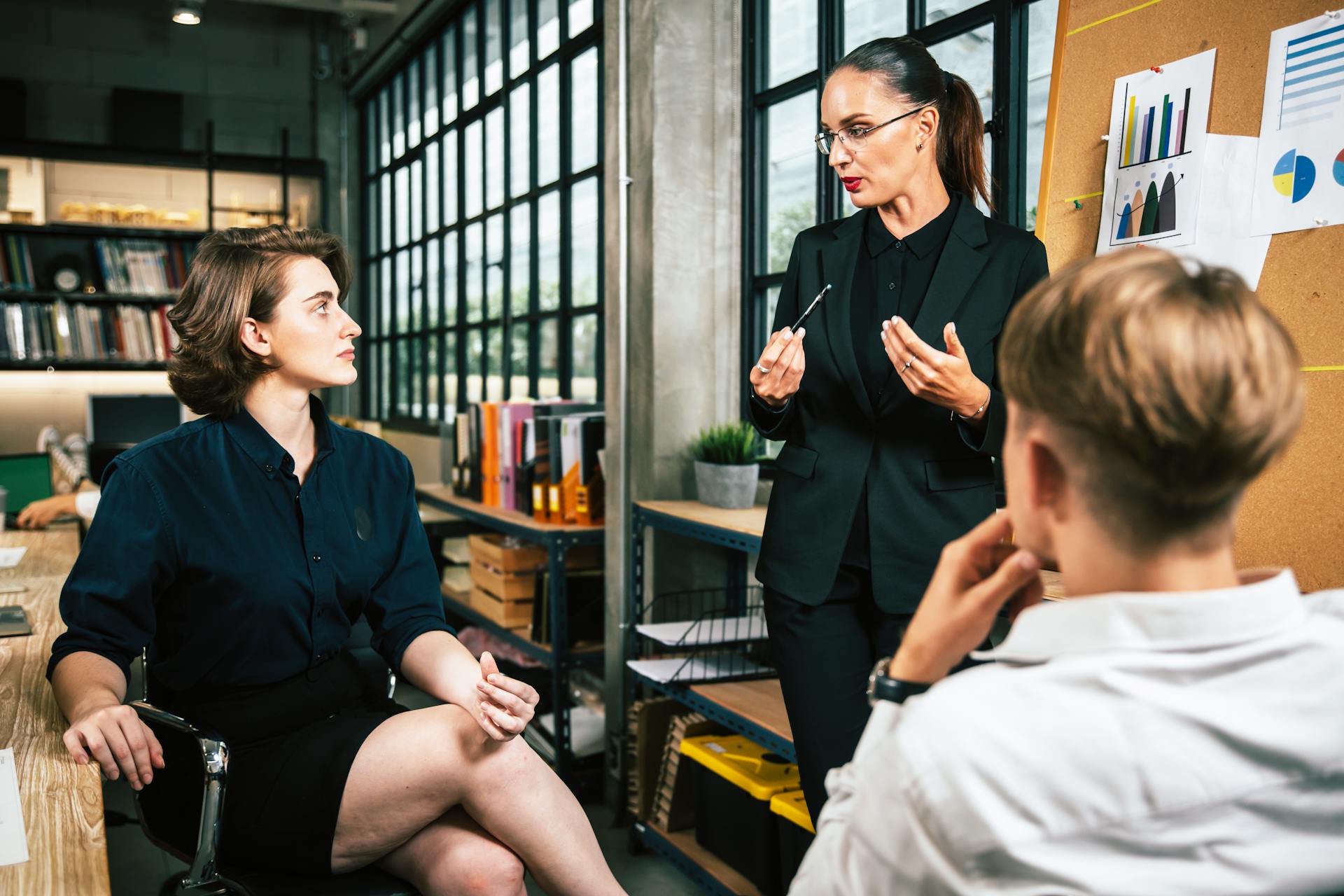
In today's competitive market, it's a challenge for firms to generate the desired revenues and profits to meet their objectives. Increased revenues and profits are a direct result of implementing Quality Management, which ensures a high level of customer satisfaction.
High customer satisfaction leads to a higher brand value, giving firms a competitive edge in the market. This edge can result in a higher market share and loyal customers.
Firms that fail to understand the importance of Quality Management often incur losses. This simple yet crucial fundamental is often overlooked, but it's essential for achieving business aims and objectives.
By prioritizing Quality Management, firms can ensure a steady stream of revenues and profits, meeting both short-term and long-term objectives.
Discover more: When Starting a Small Business It's Important to Remember
Prevention and Consistency
A Quality Management System (QMS) helps you detect problems before they happen, essentially acting as a risk management system that identifies areas of risk in your processes.
Any issues in your production or service delivery processes will be identified and logged, so they can be addressed before they affect your customers, reducing the risk of lost sales and complaints.
For your interest: Are the Most Important Part of an Information System
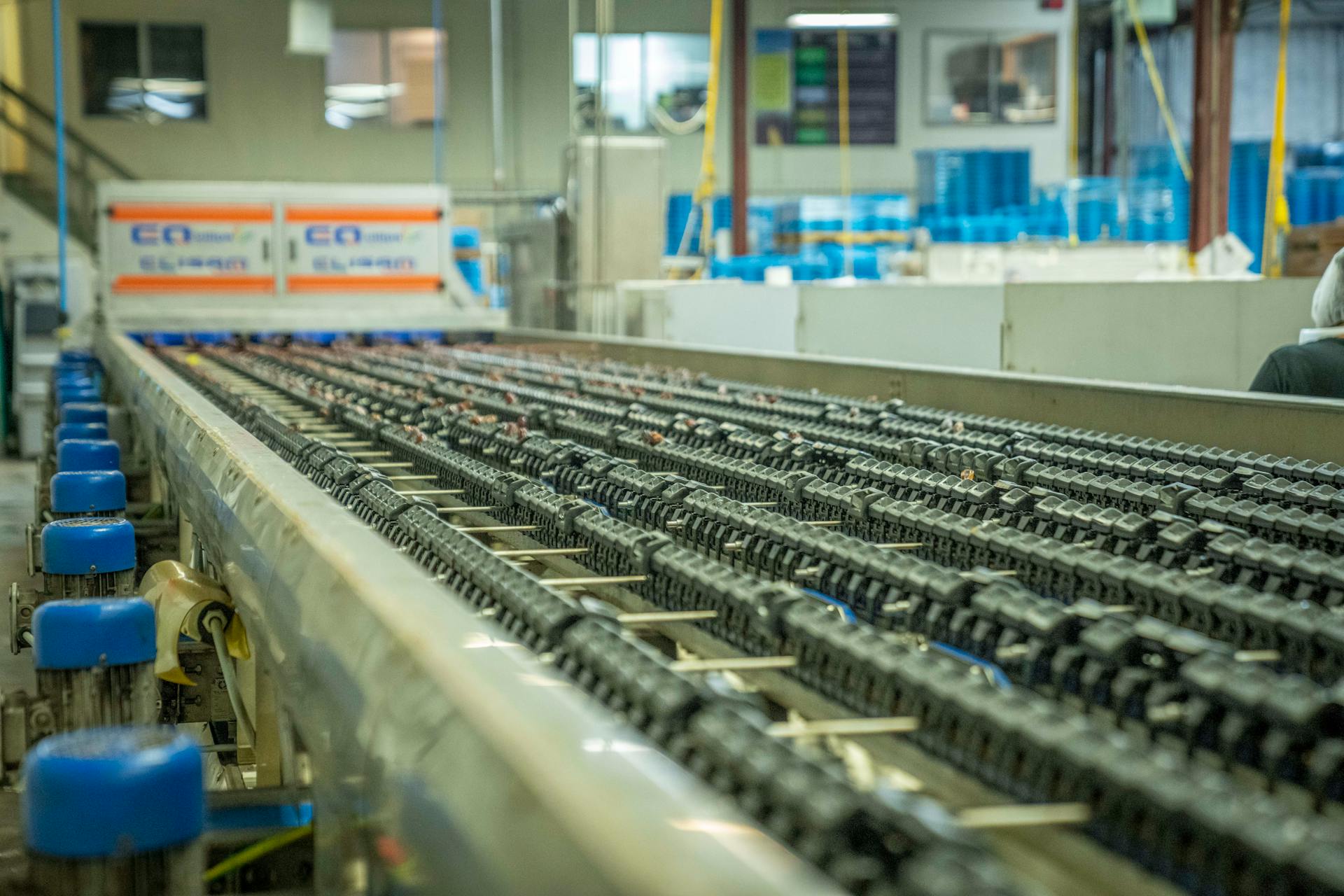
Consistent quality and make of the products are crucial for businesses, and a QMS helps firms maintain quality on a consistent and continuous basis.
By maintaining total quality management at every facet, firms can ensure their products stand as a testament to quality and its principles.
Regular market research and studies help firms drive the production of high-quality products that meet customer expectations.
Intriguing read: What Is Most Important When Developing Easy to Use Products
Frequently Asked Questions
What is the main point of quality management?
The main point of quality management is to consistently meet customer requirements by standardizing business processes. This ensures that every process is performed with the same information, methods, and controls.
Sources
- https://www.managementstudyguide.com/importance-of-quality-management.htm
- https://www.quality-assurance.com/blog/7-quality-management-principles-and-why-theyre-important.html
- https://opcentral.com.au/about/blog/post/5-reasons-why-quality-management-systems-are-crucial-to-your-business
- https://www.marketing91.com/importance-of-quality-management/
- https://www.gbscorporate.com/blog/why-quality-matters-more-than-ever-in-business
Featured Images: pexels.com